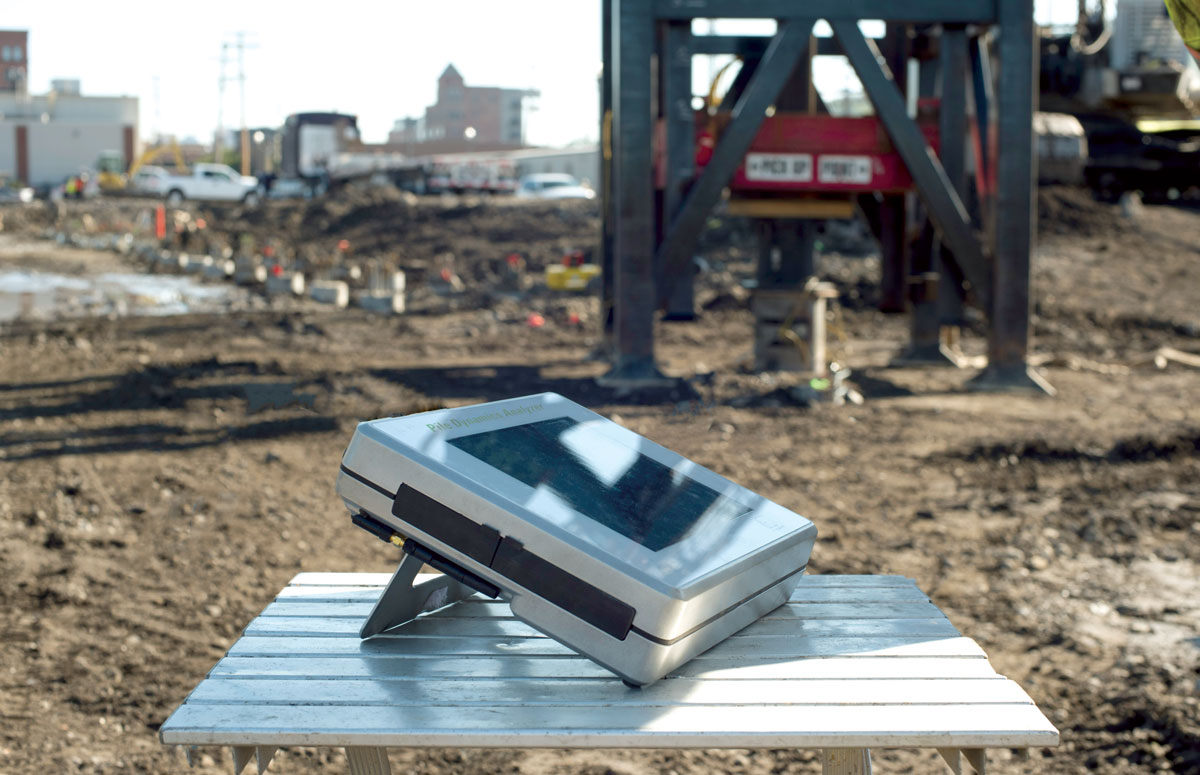
Dynamic Load Testing (DLT) is a fast, reliable and cost-effective way to test the bearing capacity of foundations. For over 40 years, the Pile Driving Analyzer (PDA) has been the go-to software for such testing. However, in 2018, Pile Dynamics, Inc., created a software add-on to the PDA that makes DLT quicker and easier than ever before.
DLT is one of two elements that make up High Strain Tests (HSTs) of deep foundations, the other being Dynamic Monitoring (DM). HSTs essentially use strain gauges and accelerometers to measure the strain and particle acceleration caused by an impact to the top of a foundation element. DM is used to measure the pile installation process by evaluating driving stresses, hammer performance and pile integrity to optimize the installation itself and reduce damage to the pile and hammer. Capacity is also calculated during the installation for each impact from the hammer and thus, the engineer can monitor capacity development during the driving sequence.
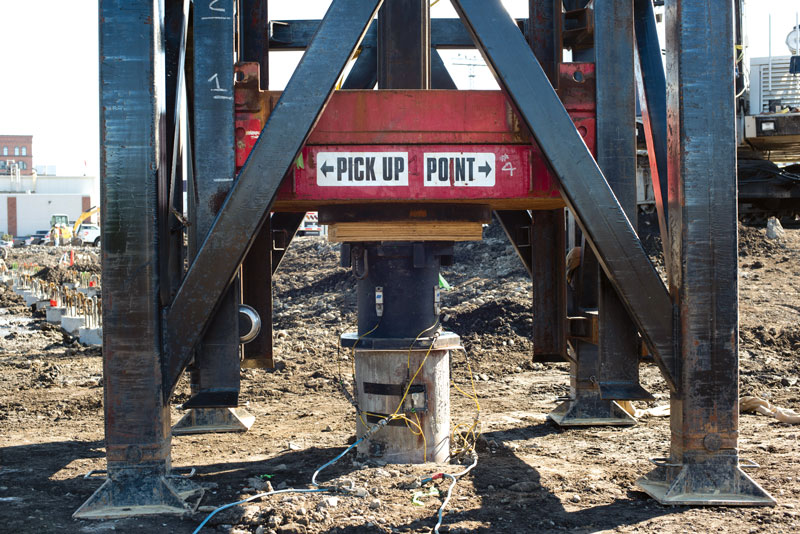
However, DM doesn’t tell the engineer everything they need to know because the resistance of the soil or partially weathered rock, calculated during pile driving, may not be reflective of the long-term resistance because of the way the soil is disturbed during driving. To obtain a more accurate reading of long-term resistance, engineers turn to DLT, which can be performed on any deep foundation element from driven and drilled piles to Continuous Flight Auger (CFA) piles.
DLT is focused on capacity, stresses to the pile, pile integrity and more, looking for either a proof load, where pile design and safety are optimized, or the ultimate load for a pile, which means potential soil failure is achieved. This is useful for refining a pile’s length or size. For 40 years, the PDA was the industry standard bearing software for DLT – collecting and analyzing data from various drilled piles over the years, such as drilled shafts/bored piles, Augured Cast-In-Place (ACIP)/CFA piles, helical piles and more.
Then, in 2018, Pile Dynamics, Inc., created the Pile Dynamics Analyzer-Dynamic Load Tester (PDA-DLT), a software add-on that works with the traditional PDA, but can also work as a standalone system. It was created to improve the assessment and summary of data during DLT of drilled piles by allowing for multiple configurations of force measurement (such as a force transducer), while evaluating bearing capacity, structural integrity and foundation stresses.
“With the PDA-DLT, we can input into the software directly the physical properties of both the transducer and the pile and the DLT software will then calculate the stress in the pile.”
Tom Hyatt, P.E., GRL Engineers
Unlike the traditional PDA, the PDA-DLT can tabulate data over multiple impacts of the pile top from the load cell – a piece of steel with strain gauges attached to measure the force of the impact on the pile below. The PDA-DLT also gives the user the ability to input the hammer’s drop height (and therefore, the energy applied to the pile top on impact), and with that data it can calculate the total permanent displacement of the pile over several impacts.
In addition, the input parameters to measure force are easier to define using the PDA-DLT than with the original PDA software. Typically, when performing DLT, a measurement must be taken at a minimum of two diameters below the pile top. Although this is generally not a problem for driven piles, it may become a serious issue for a large diameter drilled shaft. Thankfully, with a steel load cell the pile doesn’t need to be drilled into that far down, and the PDA-DLT can take an accurate measurement from a steel force transducer placed on top of the drilled shaft, which eliminates the need for excessive build up or excavation to get an accurate force measurement.
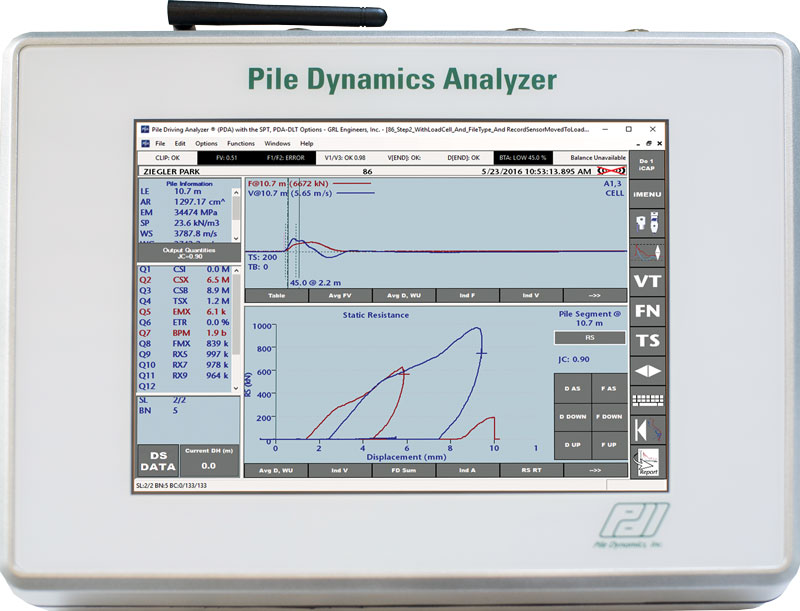
“When we use a transducer, we are measuring the strain on a steel element, which has different material properties than the pile itself and we used to have to take that into account. With the PDA-DLT, we can input into the software directly the physical properties of both the transducer and the pile, and the DLT software will then calculate the stress in the pile,” said Tom Hyatt, P.E., at GRL Engineers’ Georgia office.
The PDA-DLT works the same way as the original PDA, with its additional variables and accountings programmed in. Basically, the PDA works by measuring strain and acceleration, and then multiplying the strain by the modules of elasticity and area to calculate a force, and by integrating the acceleration to obtain a velocity. Then by using wave mechanics and signal matching software, a trained professional can assess the data to interpret mobilized capacity, stresses in the element, hammer performance and more.
“The PDA-DLT saved me multiple headaches because of the way it calculated the load set curve and the stresses in the pile along with other relevant quantities.”
Tom Hyatt, P.E., GRL Engineers
This is done by dropping a hammer on the steel load cell with strain gauges on it. At the point of impact, the whole thing compresses and the strain gauge measures how much the surface material changed in that moment. From that data point, engineers use wave mechanics and material properties to determine the force on the pile itself. The PDA-DLT is so accurate, deft and easy to use that DLT can be completed on production piles.
“Most of the time, dynamic load tests are done on sacrificial piles, so if you break the pile, it’s not a huge loss, but in 2019, I was on a project where we were doing load testing on production piles. These are piles that were meant to become part of the permanent structure,” said Hyatt. The contracted APPLE load testing project required that the seven production ACIP piles be dynamically proof load tested to a minimum geotechnical resistance of 200 tons (400 kips), without overstressing or incurring excessive permanent settlement of the foundations. The foundations were tested by applying two to three hammer impacts, ranging in heights from six inches (152 millimetres) to 1.5 feet (457 mm).
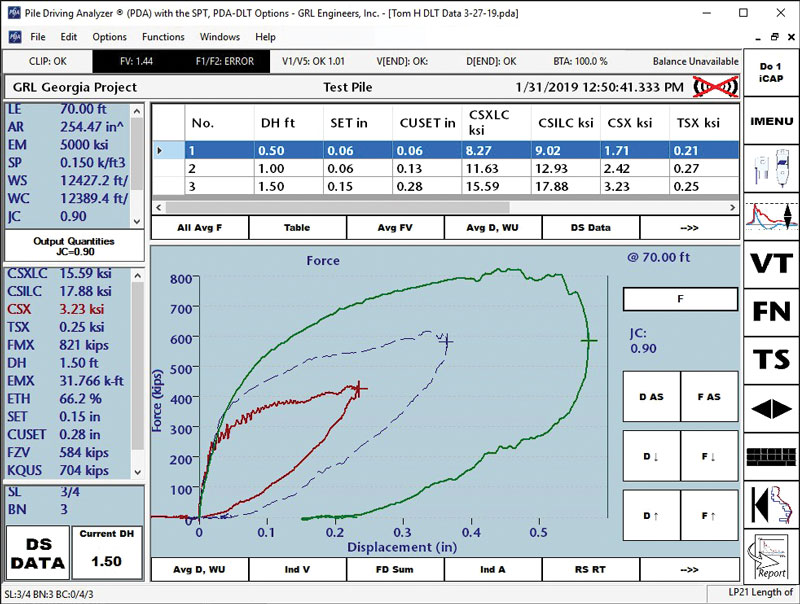
“I wasn’t allowed to over stress the piles; I couldn’t push them or have a high pile displacement because these piles still had to be used at the end of the day. Under those circumstances, the PDA-DLT saved me multiple headaches because of the way it calculated the load set curve and the stresses in the pile, along with other relevant quantities,” said Hyatt.
Without the PDA-DLT, Hyatt would have had to measure each pile’s diameter and then find the ratio between the area of each pile to the area of the steel transducer, which would give him a K-factor that he would apply to the data he gets from each impact, every single time. This way, the K-factor was automatically calculated for him which saved him time.
“The calculations can be made at a much faster rate, which saves a lot of time and effort on my part,” said Hyatt.
Hyatt’s experience confirms that with the PDA-DLT, load testing can be performed on many more complex foundations than were previously possible, while stress on foundations can be calculated with greater speed and more efficiency.