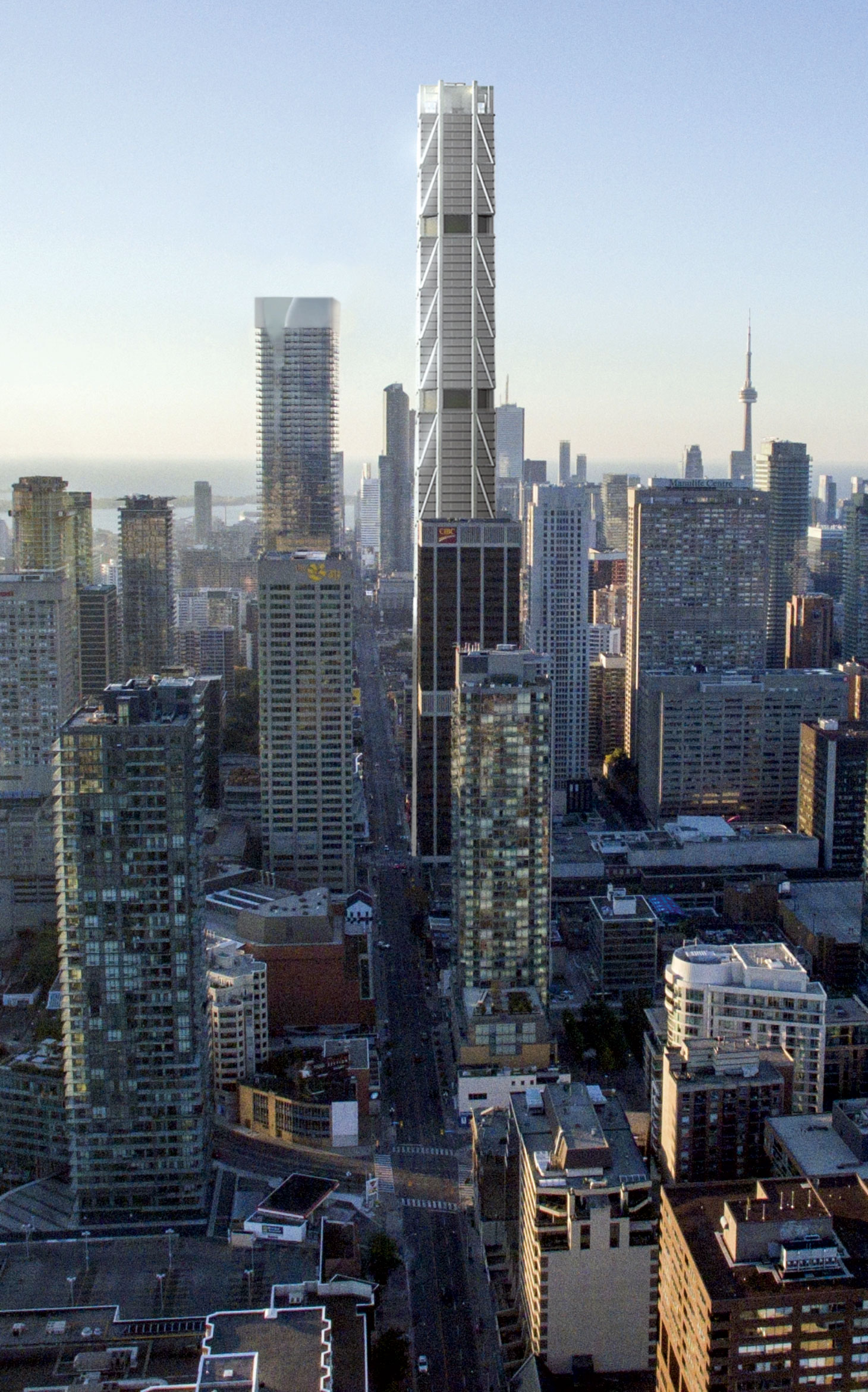
The iconic CN Tower has long been the defining landmark of Toronto’s skyline. This might change with the arrival of The One – Canada’s first and only officially recognized super tall building.
Acting as the gateway into the city’s upscale “Mink Mile” on the bustling corner of Yonge and Bloor, The One is Toronto’s first billion-dollar condo development and – standing at 328.4 metres (1,077 feet) – is set to become Canada’s tallest building, supplanting the previous record holder, the 298-metre BMO Tower at First Canada Place.
The One is a Mizrahi Development project and was designed by Fosters + Partners and CORE Architects. The project has been designed in keeping with the principles outlined in the Tall Building Design Guidelines, and the top of the building will feature distinctive cladding and subtle geometry, adding a distinct presence to the city’s skyline. The 91-storey tower rests on a 31-metre floorplate, giving the more than 1.25 million square-foot building a slender silhouette because of its height to width/depth ratio. The One has also been designed to minimize shading and wind impact to the surrounding buildings and is spaced away from other existing and planned towers.
The One’s innovative hybrid exoskeleton and super structure is comprised of a ring of eight “mega-columns” and a hanger frame along the perimeter to create its distinctive form. Fosters + Partners’ exoskeleton design places the majority of the tower’s support structure on exterior trusses rather than within the interior, allowing sunlight to penetrate the space with a minimum of obstructing columns. This will provide an airy and open space capable of accommodating a wide variety of retail and cultural tenants.
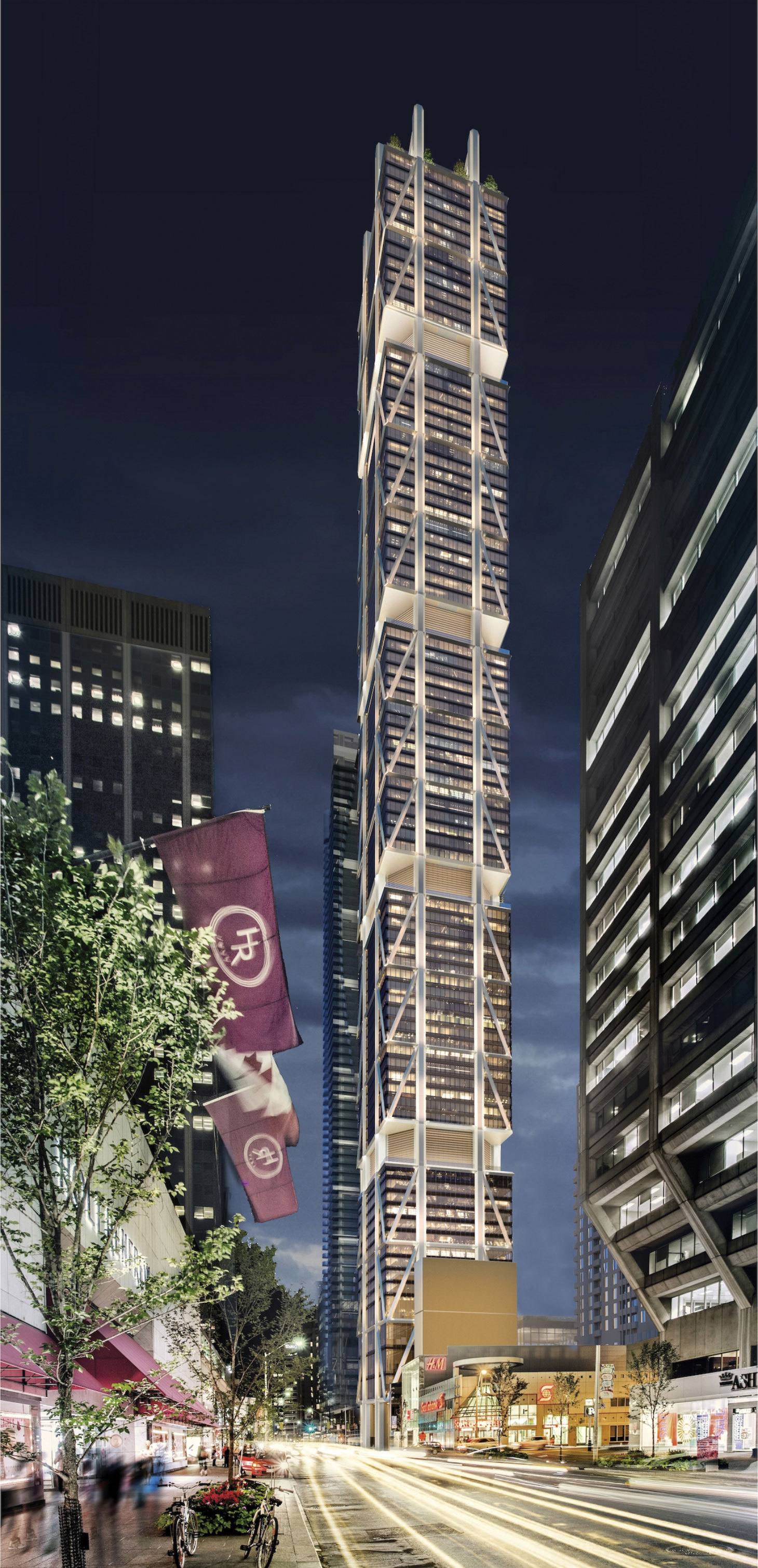
Below ground, a connection to Toronto’s Downtown Pedestrian Walkway and the subway has been designed along with parking for 600 valet spaces. Directly above the retail podium, an amenity area will be accessible by a bridge on the 12th floor for the residents of the 560 residential suites that feature floor-to-ceiling glass walls to take advantage of the unparalleled views of the city. Many units will also have “winter gardens,” and balconies that can be opened or closed to provide control of natural ventilation. The One’s exterior façade will also be lit up by an innovative, Japanese-made LED lighting system that allows the tower to glow a variety of different hues and colours.
A sustainable design
The One has been designed to fulfil the planning and urban design framework established by the City of Toronto Official Plan and the Bloor-Yorkville and North Midtown Urban Design Guidelines, which support intensification and a tall building on the site given its proximity to existing transit services. The project also fulfills Official Plan goals to promote mass transit and pedestrian modes of travel, and reduce private automobile dependency.
Located at the crossroads of the city’s two major subway lines, The One’s P1 retail concourse provides an indoor air conditioned environment with access to public transit. The bike-parking ratio conforms to Tier 2 standards and is conveniently located in an underground mezzanine above the P2 parking level.
The large native tree canopy exceeds Tier 1 requirements for shading of on-site walkways. Street trees are located to clear underground utilities and allow for continuous soil trenches that meet Urban Forestry requirements for soil volume. Fritted glass is also strategically placed throughout the elevations of the tower to help avoid bird collisions. Along with this enhanced bird-friendly glazing, overhangs will further contribute to the reduction of collisions.
Reaching new heights needs a good foundation
Excavation at The One commenced in 2015, followed by a gradual buildup of heavy machinery in the months leading up to the mega caisson drilling, including a heavy-duty Link-Belt TG2300B crane and a Bauer BG 55 (BS 115) drilling rig. This allowed crews to begin working on the massive underground columns that support the building’s unique hybrid exoskeleton structure. The BG 55 rig was used to drill eight 3.65-metre caissons 30 metres deep from the base of the excavated pit. Once the boreholes were drilled, massive rebar cages weighing approximately 40 tonnes each were lowered in by the TG2300B crane, and then filled with 378 cubic metres of concrete to form the caissons.
“The rebar congestion was a major hurdle for us to overcome,” said Rebar Enterprises’ Emin Buzimkic. “On a typical project, the rebar and structural steel comprises about four to eight per cent of the total column. For The One it was about 20 per cent and the position of each bar was measured in millimetres.”
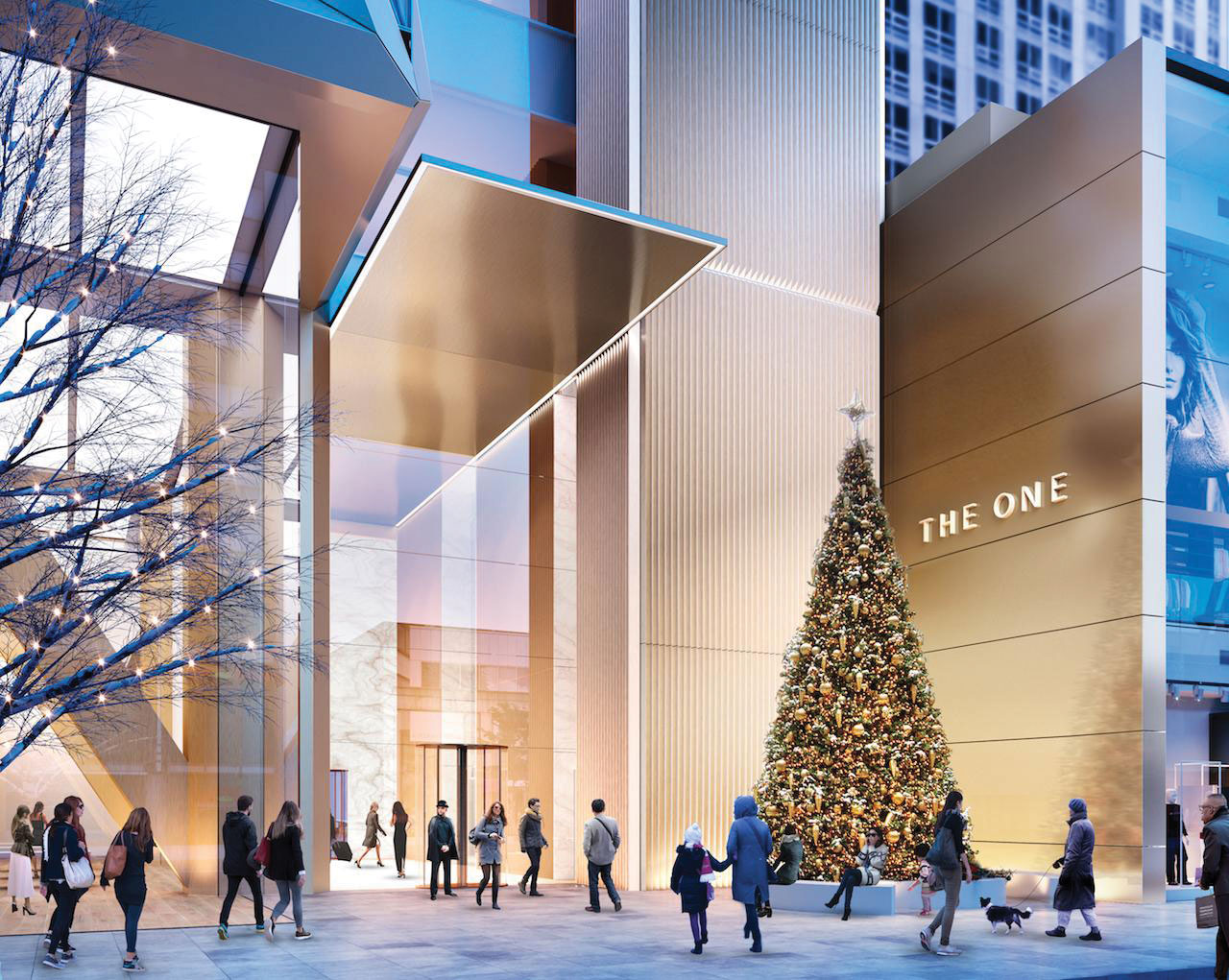
Modular Re-Bar, with its pre-fabricated and assembled design, offers significant advantages for green buildings and sustainability initiatives. Its streamlined manufacturing process reduces material waste, energy consumption and on-site construction time and, by optimizing rebar placement and minimizing errors, Modular Re-Bar enhances structural integrity and reduces the need for additional materials and resources. Rebar Enterprises holds the patents for this kind of modular pre-fabricated rebar, which has become the industry standard for construction in the Greater Toronto Area. This innovation eliminates much of the need for rebar cages to be woven and welded amidst an already busy construction site, using the combination of on-site assembly and a fabrication facility.
“This innovation aligns perfectly with green building principles, contributing to lower carbon footprints and improved resource efficiency,” said Buzimkic. “As Rebar Enterprises embraces this approach, we position ourselves as leaders in sustainable construction solutions, gaining a competitive edge in both the Canadian and global markets.”
Building the sky
A pivotal technology used to overcome challenges in the construction of The One has been the Otis SkyBuild, a self-climbing lift system that “grows” with the building. For this project, Otis Canada supplied 23 elevators to the site, marking Otis’ first installation of its SkyBuild construction elevator in Canada. The company provided 11 SkyRise elevators, eight Gen2 elevators and four SkyBuild construction elevators, which permanently convert to the SkyRise tech-smart elevator system once construction is complete.
“The most important and decisive factor that led us to work with Otis for this ambitious project is the SkyBuild elevator’s ability to execute its floor climbs during off-hours – we’re simply able to show up for work the next day ready to go,” said Joshua Lax, vice-president of development at Mizrahi Developments in a press release.
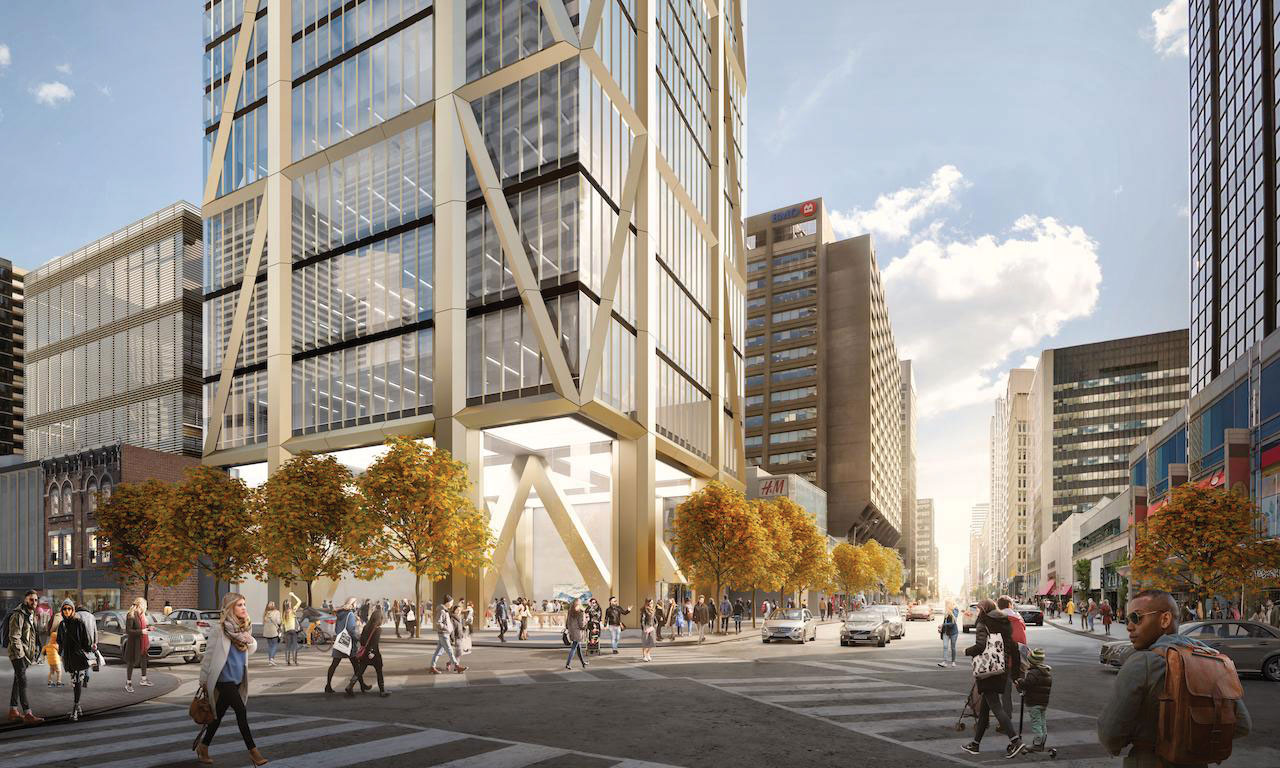
SkyRise elevators – Otis’ high-rise platform – delivers speeds up to 12.5 metres per second and climbs up to 600 metres. The Otis Gen2 elevator platform is redefining the industry with its unique, patented flat-belt drive technology that replaces conventional ropes and significantly reduces vibration, providing passengers and tenants a remarkably smooth and quiet ride with improved overall comfort compared to more conventional systems.
“It’s an honour to provide the technical expertise and products for the tallest building in Canada,” said Jim Cramer, president, Otis Americas. “We thank Mizrahi Developments for placing their trust in Otis and for the opportunity to showcase the benefits of our SkyBuild elevator on this important project.”
The One’s unique Rail Climbing System (RCS) has also helped lead to the overall success of the project and has allowed contractors to continue working on the tower’s exterior, even after the grade-level retail unit was opened to the public. The RCS also keeps the perimeter of the building clear of clutter for the safety of pedestrians. Rather than having materials and workers hoisted up from ground level, the RCS ensures that any hazards along the street level are absent.
The RCS was installed across the tower’s north, east and west elevations, with a different system installed on the south elevation to work around the crane. Construction of The One is expected to be completed in 2024.
IMAGES: FOSTERS + PARTNERS AND CORE ARCHITECTS