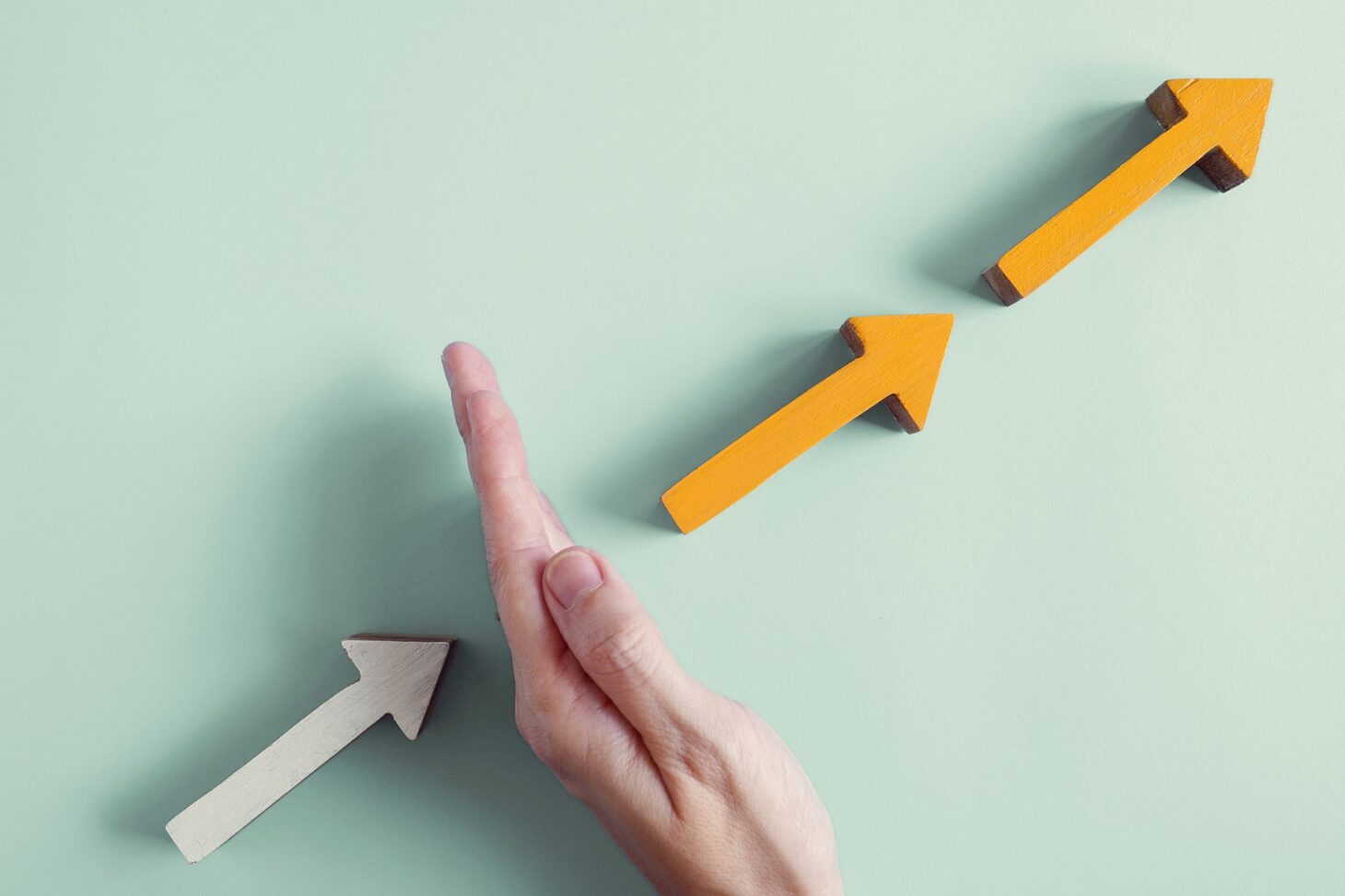
According to insurance company HUB Canada’s 2023 Construction Outlook, supply chain issues will continue to challenge the construction industry this year, remaining unpredictable and causing disruptions to cost management and scheduling.
“COVID-19 really impacted the construction industry’s supply chain, which is still felt today,” said Nick Pettengill, construction support manager at Raken, which provides businesses with construction management software to streamline their project management and communication processes. “Meanwhile, inflation, labour shortages, poor weather conditions and new international import and export regulations have also compounded the problem.”
Inflation remains a huge challenge for the construction industry, and HUB predicts that ongoing materials shortages, from roofing membranes to electrical equipment, will continue to hamper construction and profits. A construction business’ bottom line can suffer from common supply management errors, such as inventory miscounts, faulty calculations, delivery miscommunications and billing errors.
“A single supply management error can cost construction businesses thousands of dollars or more in lost revenue,” said Pettengill. “Especially when the issue isn’t caught and corrected in a timely manner.” Whether the cost stems from the error itself or results in a production delay, timing is everything. “When a supply management issue is identified, the method of resolution depends on the type of error,” said Pettengill. “However, no matter what the problem is, a review of past data is likely needed before the error can be corrected.”
For example, if a business notices that a supplier has been overcharging the amount on a recurring payment, to receive their full refund, they will need to provide invoices for each instance the company overcharged them.
“Likewise, if an employee accidentally enters the wrong number into a tracking system and inventory is miscalculated, a supply manager will have to track down when the error first occurred to determine how the business has been affected,” he said. HUB calculates that only seven per cent of construction firms use software solutions and should consider adopting new technology to improve processes.
Construction companies can
prevent supply management issues by putting the right technology into the right hands.
“Automated supply management tools minimize human error and significantly reduce the time it takes to accurately track inventory,” said Pettengill. “Still, there’s no discounting human oversight. Technology can fail, and supply chain professionals must continuously monitor any automated processes.”
Pettengill says the software also can’t replace humans’ interpersonal skills. “Supply chain managers navigate supplier relationships, making these roles essential to construction businesses.” Pettengill says that construction companies can prevent supply management issues by putting the right technology into the right hands. “It’s essential to identify managers who have developed a blend of analytical and soft skills,” he said. Technology such as automated production tracking, warehouse management and resource management tools help managers avoid mistakes by automatically tracking inventory and identifying discrepancies, while digital daily reporting tools can help businesses make more informed scheduling and purchasing decisions from the start of a project.
“Software organizes and calculates information much more quickly and accurately than manual methods,” said Pettengill. “But choosing the right technology and the right person to optimize the inventory management process while also maintaining good working relationships with suppliers is imperative.”
He says employing a good supply management process is vitally important to profitability. “With the rising cost of materials and fluctuating delivery time, construction companies must be especially conscious of managing their inventory to avoid costly delays,” he said. Pettengill also says good supply management practices help construction companies optimize their resources. “With a thorough understanding of their existing inventory, as well as the billing and delivery process, businesses can better plan projects and make more informed purchasing decisions,” he said.
Pettengill says businesses should also look at digital tools that enhance the daily reporting and documentation process to help them better manage inventory and project progress. “There are digital tools that include capabilities like photo and video capture, and instant data sharing will help supply managers see how materials and equipment are being used onsite in real-time,” he said. “With production-tracking software, field contractors can more easily and consistently track material use on-site. Because digital tracking methods save significant time over pen and paper, they’re more likely to meet reporting requirements on a regular basis.”
Pettengill says digitally recorded data can also be shared instantly with supply managers and automatically organized into easy-to-understand formats like charts and graphs.
“Supply managers can visually see how much of a certain supply or material they use in real-time and order more when necessary, or use those insights to plan future projects.” Digital tools can standardize the supply-tracking process and leave little room for manual error. “Digital tools don’t replace your current staff or processes; they should enhance them,” said Pettengill. “Good technology helps your staff save time on repetitive tasks and focus more on tasks that require their unique skill sets. It’s a win-win situation.”