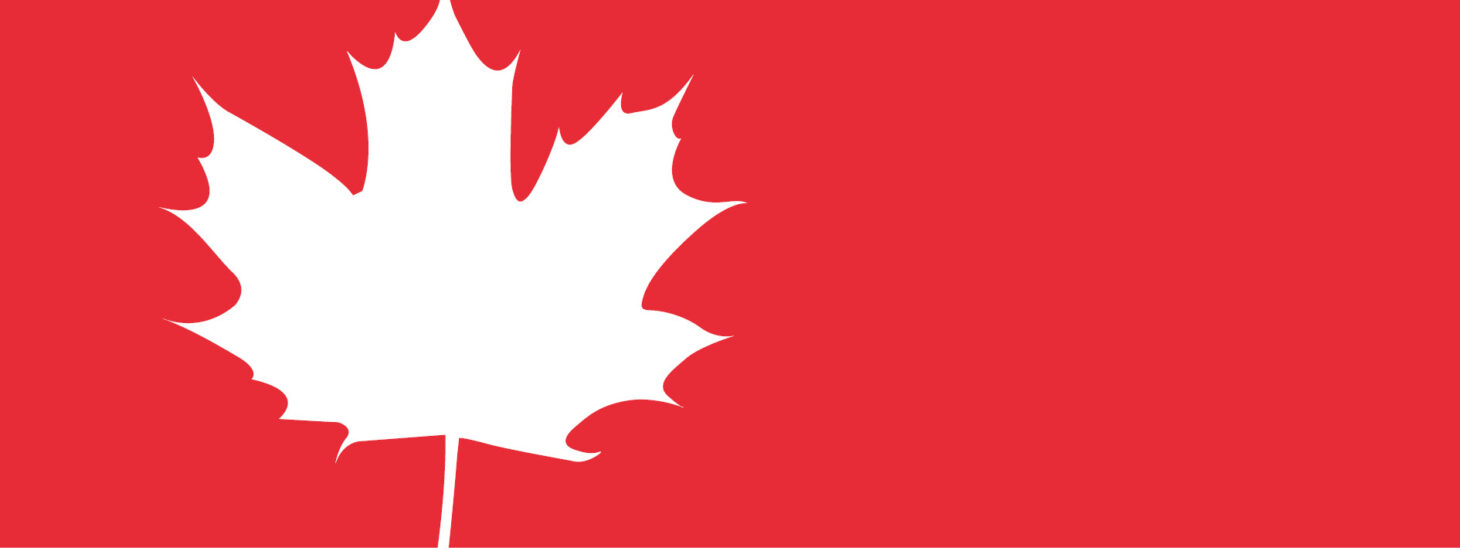
GeoRocFor celebrates 30 years of drilling and new success in its XS overburden systems
If you ask the folks at GeoRocFor Inc. how business is doing, they like to say they’re “getting through the toughest conditions.” That’s not because business is bad – quite the contrary: the Sherbrooke, Que.-based company is celebrating its 30th anniversary in 2015 as a leading manufacturer of drilling tools and an industry leader in overburden casing systems.
In the early 1980s, company founder and current president Roger Charland was working as a sales representative for an equipment distributor in Montreal, handling heavy drilling machinery, but not
consumables like drill rods and bits. Seeing a niche, Charland launched GeoRocFor Inc. in 1985.
Initially, many of the new company’s products went to a fairly narrow range of customers, including foundries.
“Then, because the products are similar, we started to cover the construction segment of the drilling sector, including blasting,” said Roger Charland’s son, GeoRocFor operations manager, Luc Charland.
It’s a big market, he says.
“But it’s a difficult market, because [like] everything related to construction, the prices are very competitive, so in 1990 we started manufacturing some of those accessories for the industry.”
As the client base started to shift, the company began to concentrate on down-the-hole hammers for the pilings and water well drilling industries, manufacturing products like drill bits, drill rods for water wells, casing shoes and threaded casings.
From the beginning
Starting with a staff of four in 1985, GeoRocFor now employs 18 people, including five in the office, two technicians and 11 in production. Operations were based in a succession of rental spaces until 1997.
“[Then,] we built our factory,” said Charland. “Six years later we built an addition to that main building.”
One of GeoRocFor’s biggest breakthroughs came with the 2007 development of its XS overburden drilling system.
“There are only a few competitors worldwide with that kind of full-face casing system,” said Charland. “Compared to the wing-type overburden casing system, this has a full crown and drills like a standard bit.” The only two firms with a comparable product are based in Finland.
“I designed it myself,” said Charland proudly. “We improved it a lot with different research and development programs over the years.”
Originally, it was suited for the needs of water well contractors, but “then we realized that foundation [construction was] 95 per cent of our potential business; on one job site they could install 200 casings – but they are shallow, 40 to 60 feet in the ground.”
{fastsocialshare}
Constant evolution
With the help of the federal and Quebec governments, the company was able to improve the quality of the system, and now GeoRocFor is now established as the leading specialist in overburden drilling applications; they offer nine different systems, each adapted to a particular need.
“We’re world leaders – not in numbers, but from the technical point of view. When a customer calls us, they can have access to me, to Roger or to one of our technicians,” said Charland. “They can have the real answer; they can adapt any system to a very specific need.”
GeoRocFor’s XS-GT (Go Through) system has been used in numerous notable and challenging construction projects in recent years, like the 2011 foundation work for two bridges on Autotoute 73 in the Beauce region of Quebec. One bridge, crossing the Famine River, measures 148 metres across, while a second over the Gilbert River is 325 metres long and 170 metres high. Carried out by Pétrifond Fondations under the auspices of Quebec’s Ministry of Transportation, the jobs required 130 twenty-four-inch diameter piles drilled into bedrock to depths between 45 and 70 metres.
Another exciting project for the XS-GT system was last year’s installation of a three-megawatt wind turbine at Glencore’s Raglan Mine on the Ungava Peninsula in Nunavik, about 1,800 kilometres north of Montreal, carried out by MSE Drilling. Canada’s first industrial-scale wind and energy storage facility is expected to replace approximately five per cent of the mine’s diesel consumption.
Looking ahead
“We are proud that we are manufacturing down-the-hole casing systems and drill bits in Canada. There are not a lot of other manufacturers who are able to do that in Canada. We’re very proud of that, and of being able to understand every stage of the use of a casing system, so we can continue to adapt and come up with other new systems in the future,” said Charland.
Well established across North America, the company has become a familiar face at deep foundation industry events, such as the International Foundations Congress and Equipment Expo (IFCEE).
“What we like about this exhibit compared to others is that the focus is really on piling,” said Charland. Along with its large North American client base, the company also exports to South America, Europe and Asia. GeoRocFor has been the largest supplier of drilling systems in Spain for umbrella (tunneling) applications.
Charland is optimistic about the future of the industry in Canada and the U.S., due in part to seismic regulations. “We will see more and more drilled piles, so I guess that will be a market that will be growing,” he said.
And GeoRocFor is still innovating.
“We’re still continuing to come up with other new drilling products; I’m working on other prototypes at the moment,” he said. Also, in 2014, the company got together with a group of specialists in collaboration with the National Research Council of Canada (NRCC) and the University of Sherbrooke to explore new and better drilling products by using computer simulation to virtually “watch” the action of the drill underground.
“We’re trying to develop a simulation – a model – so we can predict what will happen in the ground and improve the quality of the systems,” said Charland. “It’s like putting eyes in the ground, where we cannot usually see.”
This analysis will help GeoRocFor customize its products to match the precise needs of its customers, which means that, over the next few decades, the company will be able to “get through the toughest conditions” even more efficiently.
{fastsocialshare}