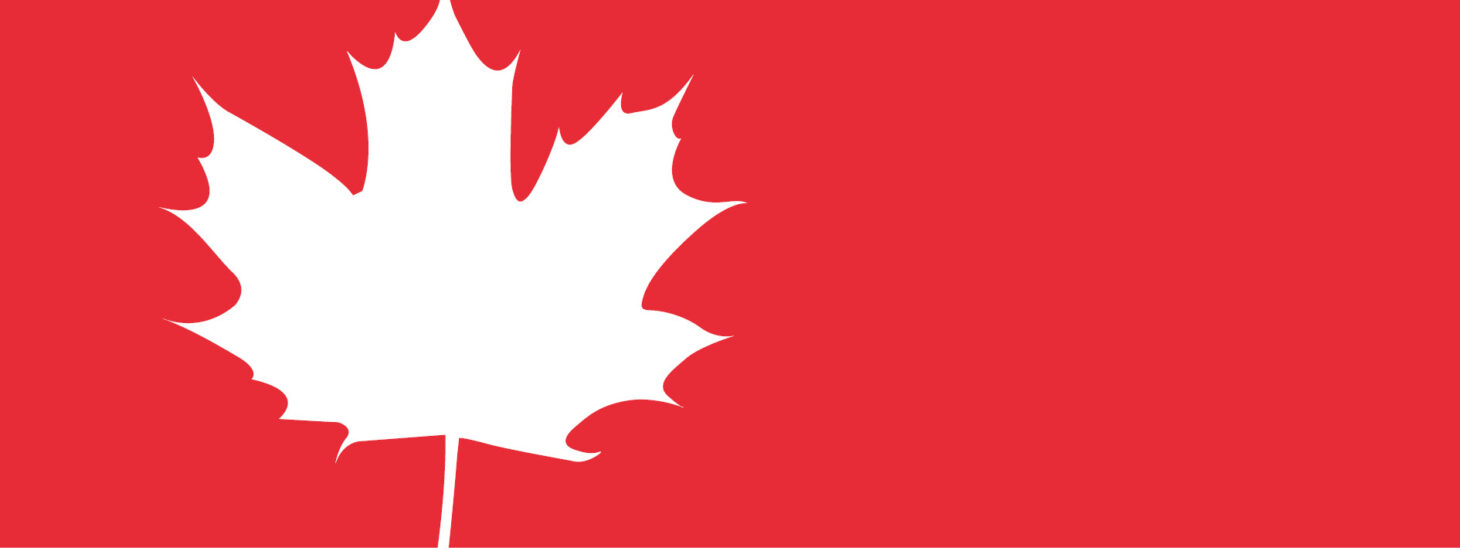
At the end of October, Liebherr-Werk Nenzing GmbH invited me to attend their annual Liebherr Information Tour for the International Construction Trade Press. The event took place over the course of a few days in Germany and France, with about 40 participants from 13 different countries from the around the world. Piling Canada was the only Canadian publication represented.
On Oct. 22, I flew from Winnipeg, Man. to the airport in Frankfurt, Germany. After lunch, our group took a bus to Darmstadt, the location of the construction of a new particle accelerator, the Facility for Antiproton and Ion Research (FAIR) in Europe. Professor Boris Sharkov, the scientific managing director at FAIR, Dr. Markus Bernards, public relations officer at FAIR, Dr. Florian Hehenberger, director of site & buildings at FAIR and Johannes Rhomberg of Liebherr explained the facility, the building process and equipment technology of the impressive construction undertaking.
FAIR: the project
FAIR will be one of the world’s largest research facilities. The project, expected to cost around 1.6 billion euros, is being funded by international shareholders; the Federal Republic of Germany together with the state of Hesse is assuming close to three-quarters of the cost, with remaining shareholders responsible for the rest. Such a massive project can only be realized with international cooperation, and among FAIR shareholders are Finland, France, India, Poland, Rumania, Russia, Slovenia and Sweden, as well as Great Britain, an associated member of FAIR GmbH.
Following the anticipated completion date of 2018, scientists will use the particle accelerator to examine the development of the universe, from the “big bang” to today. Other plans for the facility include developing new medical therapies and diagnostic methods as well as energy-efficient high-performance computers and new materials ( for interplanetary space travel, for example).
More than 3,000 scientists from around the world will visit FAIR each year once the construction is complete to conduct a wide range of experiments, focusing on questions surrounding the building blocks of matter, such as the origin of elements or how matter reacts under extremes of pressure and temperature.
Such a sophisticated purpose requires a sophisticated building. A ring accelerator with a circumference of 1.1 kilometres will form the heart of the FAIR complex. 24 buildings and tunnel sections will provide more than 62,000 m2 of usable space and enough room for 3.5 kilometres of beam control tubes and huge detectors with complex technical infrastructure. Approximately 35,000 tonnes of steel and 600,000 m3 of concrete will be used to build the facility. At peak times, as many as 600 construction workers, technicians and engineers are employed on the site. This heavyweight construction – with metre-thick walls, in some places – requires solid foundations. Liebherr machines were the choice foundation equipment.
Challenging ground conditions
Geotechnical engineers carried out extensive preliminary subsoil surveys to learn about the composition, as it plays a key role in determining settlement behaviour. In all, the structures should settle as evenly as possible within a predictable timeframe. 68 exploratory bores were drilled at depths between 35 and 80 metres, while more probing tests were done with a heavy penetrometer to determine how compact the soil was. More tests for further site compactness, consistency and permeability were completed to establish how groundwater levels will rise and fall. In all, 250 soil samples were taken and examined to predict settlement behaviour.
The geotechnical engineers discovered that the first 20 metres of the subsoil consisted of sand and silt, while clay was found up to a depth of 75 metres. These layers are largely composed of compressible materials – their density changes when subjected to heavy pressure.
Additional exploratory tests were completed between August 2011 and January 2012; three pile load tests on 22-metre (maximum) bored piles at different depths demonstrated how the piles would behave under the pressure of the heavy buildings. A five-metre-high trial embankment on a 20 by 20-metre surface was monitored for six months. In conclusion, the load exerted by the buildings on a foundation base would result in medium-range settlement of between 10 and 35 centimetres.
Foundation design to reduce settlement
The geotechnical engineers determined the load-bearing performance and deformation behaviour of the subsoil using 3-D finite element calculations, which inspired the final foundation design. The final design consisted of a combined pile-raft foundation for all facilities apart from the accelerator ring. An advantage of this foundation compared to a plain base foundation is that settlement-over-time behaviour is usually less pronounced with this type of foundation. In the case of the FAIR complex, the buildings will be more or less settled one year after the construction work is completed.
The equipment
The first two Liebherr LB 44-510 rotary drilling rigs were employed in FAIR’s construction. First revealed at BAUMA 2013, the LB 44-510 rotary drilling rig is the latest development in Liebherr’s range of deep foundation products and expands the proven LB series of rotary drilling rigs.
The lead contractor is the FAIR Bohrpfähle joint venture, comprised of Züblin Spezialtiefbau GmbH (engineering management) and Max Bögl GmbH & Co. KG (commercial management). Along with other drilling equipment, each company provided an LB 44-510 to the joint venture. With a torque of 510 kNm, the LB 44-510 is the most powerful rotary drilling rig in operation in Germany. In kelly drilling applications, it is configured for drill- ing diameters of up to three metres and depths of up to 92 metres. The rig weighs about 170 tonnes. The two rigs on the FAIR construction site were used to stabilize the subsurface with cast-in-place drilled piles.
Despite the size, the LB 44-510 rig does not require much time for its set-up. As the leader can be folded back for transportation with all hydraulic hoses connected, no disassembly is needed when moving between two job sites. Subsequently, it can be set up using the quick assembly system – barely requiring more time than smaller machines. On the FAIR site, the two rigs were ready for operation in just six hours.
The machine is also straightforward to transport. If required, it can be disassembled so that no single unit weighs more than 40 tonnes, which means it can be transported to locations around the world without problems.
The basic concept of the LB 44-510 follows two proven principles. First, this includes a large operating area thanks to parallel kinematics. Another aspect concerns the direct assembly of all winches on the leader, which allows for a direct view from the operator’s cab to the main winch as well as ensures the ropes won’t move while the leader is being adjusted. Second, the undercarriage has long crawlers, increasing stability and guaranteeing a small swing radius that can only be matched by the smaller units of the LB series.
The LB 44-510 is also suitable for drilling processing employing a double rotary head, continuous flight auger and full displacement tool. The powerful rope crowd system, with a full force of 56 tonnes, allows the entire length of the leader to be used. This gives the operator maximum performance and reliability, even on the most difficult soils and under extreme operating conditions.
Drilling great depths
In total, 1,400 foundation piles, lengths varying between 40 and 62 metres, have been set in the ground since March 2013. All drilled piles are installed down to the final depth completely cased – meaning that the excavated material is removed under the protection of an advanced casing. Due to the high groundwater level and partially unstable ground, a water load is needed throughout the pile manufacturing process to stabilize the bottom of the boreholes.
A drill bucket was used to loosen and remove the drill cuttings. The efficiency of the rigs working in the rotary drilling method means the boreholes could be excavated down to the final depth completely cased without needing a casing oscillator. In the past, two duty cycle crawler cranes with casing oscillator were required to reinforce the piles and for concreting in order to reliably guarantee the necessary torque and pull force when extracting the casing during concreting work. The LB 44-510 provided for substantially better productivity when installing piles to great depths.
Working in a drinking water protection zone also meant special requirements when preparing the piles; around 30 piles are fitted with sophisticated measuring equipment for monitoring the forces on the piles and any subsidence.
The Liebherr Group
The following day, Liebherr hosted an impressive press conference in Ettlingen, Germany focusing on their Components division, the most recent division, having been consolidated in 2007. Of crucial concern to the company is corporate independence, as well as the highest quality of products for customers.
Manufacturing its own components allows for Liebherr to master key technologies in-house, giving total control over the technological aspect of all products. No compromises have to be made, and Liebherr can offer its customers with tailored solutions for any projects. Today, the Components division employs approximately 3,250 employees on three continents.
Liebherr also has been making strides in the Combustion Engines sector. All Liebherr engines feature up to four auxiliary drives and are optimally adapted to the application concerned, including their deep foundation equipment. Due to emission legislation in Europe and North America, Liebherr accepted and has conquered the challenge to develop engines with lower emissions while retaining a higher performance.
The Reman program
During the press conference, Kurt Schoellenberger, managing director of Liebherr-Ettlingen GmbH, spoke about the Reman program. The Ettlingen site is a remanufacturing (“reman”) competence centre that employes roughly 200 workers.
Liebherr has always taken its machines to market with high quality standards – the target operating life of a Liebherr construction machine is over 25 years. Once a machine reaches a certain age, regardless of care, signs of wear are to be expected, particularly on drive components. At a certain point, repair is not cost-effective.
Liebherr offers reman of certain components with the stipulation that a remanufactured component must be on an equal level with a new component. After a component is delivered, it passes through a high-pressure pre-cleaning process before being completely disassembled. Any parts that cannot be used are disposed. The remaining material is cleaned thoroughly, paint is removed and diagnostics are run. At this stage, each individual part is examined under stringent tolerance criteria and then a decision is made on whether it’s suitable for reuse. Liebherr provides the same guarantee for remanufactured components as they do for new components. Since, in comparison with a new product, reconditioned components cost only 70 per cent of the price and require up to 75 per cent less energy and raw materials, the process is beneficial both economically and environmentally.
After the press conference concluded, we were able to take an in-depth tour of Liebherr’s Ettlingen reman facility. Due to lengthy transport times and customs and export barriers, Liebherr has been looking to establish other continental reman operations, including one in Burlington, Ont.
Tower cranes
On the last day of the trip, Liebherr transported our group by bullet train to Paris, France to view the construction site of the Canopée Les Halles, one of the most important centres in Paris, housing an underground shopping mall, Europe’s busiest underground station (with 750,000 passengers every day), various cultural and leisure facilities and a pedestrian area (with 300,000 pedestrians daily).
Several Liebherr tower cranes are being used to construct the mega-project for the City of Paris, including the visually spectacular Canopée.
Conclusion
In addition to packing the schedule with informative site and facility tours, Liebherr also treated participants in the tour to an evening at a casino in Baden Baden, Germany, where we were served a fantastic dinner and learned the basics of French roulette. I returned to Winnipeg (in one piece, even) on Friday, October 25.
For more information about Liebherr, visit their Canadian website at www.liebherr.ca.