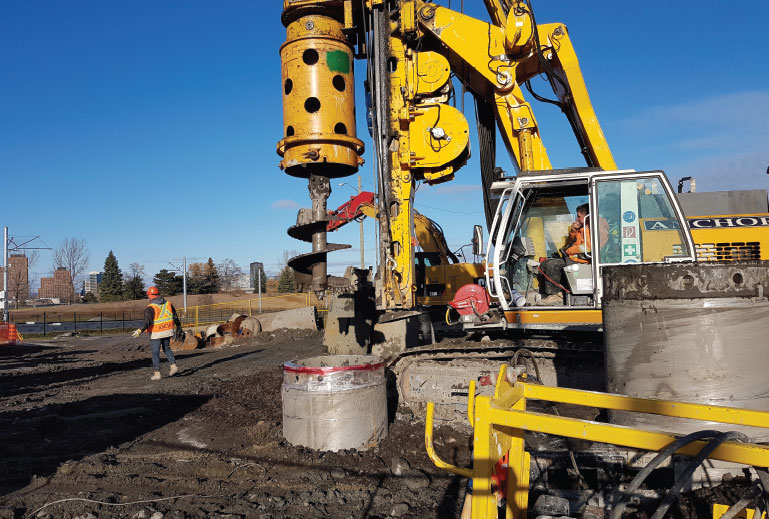
In the last article, we covered the relationship between projects and risk. In this is the third and final installment, we will discuss the right way to manage geotechnical risk as it pertains to high-risk projects.
The first item that should be discussed is the geotechnical investigation itself – which should be done first (or at least early) on any planned construction project. Standard Penetration Test (SPT) investigation methods are a “tried-and-true,” 100-year-old technology which have been, and should be, the backbone of most geotechnical investigations. Unfortunately, more often than not, SPT becomes the sole method of investigating for all soil conditions, regardless of the size or complexity of the project. It’s true that SPT is indeed an excellent way to collect some soil samples, check lithology and provide qualitative strength data.
However, SPT does come with some rather significant limitations with regard to specific soil types, and is often fraught with potential machine and human error including drilling method errors, hammer efficiency errors, soil sampling disturbance errors, drill type errors, mathematics or interpretation errors, to list a few.
There are numerous investigation methods that need to be applied correctly to ensure a project’s investigative stage is conducted in the most thorough and risk-adverse way possible based on the unique geotechnical conditions of the area (e.g. soft soil versus hard soil) and complexity of the project (e.g. low-rise building versus bridge). There are methods such as geophysical surveys, piezocone (CPTu), pressuremeter, dilatometer, direct shear, triaxial testing, consolidation testing, among others, all of which supplement a conventional investigation that is based on SPT. Dependent on the unique circumstances of a project, one or more of these methods should be included in the scope of the geotechnical investigation for a truly reliable design that mitigates underground and structural risk.
An important way to control the cost of a geotechnical investigation while reducing risk is to undertake staged or phased geotechnical investigations, by which a smaller scope initial investigation provides clarity on the second phase of an investigation that may incorporate more advanced testing techniques targeting issues highlighted in the first phase.
Phase II perhaps incorporates more than one investigation technique to further drill down on items of interest identified in Phase I. Often early geotechnical investigations do not encapsulate the full intention of the project scope as it may still be in development. A Phase II investigation later in the project cycle can help to capture the importance of any design development that may have happened and can help instruct further investigation (i.e. bigger structures with more basements may require deeper geotechnical borings in Phase II).
As positive as managing geotechnical risk can be to an owner’s bottom line, excess conservatism in design can negatively affect the bottom line. Unlike geotechnical risk, excessive conservatism usually goes unidentified, and owners often don’t have any idea how much money is wasted. When the scale and/or quality of geotechnical investigation is low, contractors can easily over or underestimate the cost by as much as 30 per cent! If there is not enough data to properly manage risk or accurately estimate the project’s construction, don’t expect a cutting-edge design to lower costs. Unfortunately, unlike geotechnical risk, there is no reliable study to determine how much money is lost on overly conservative designs.
There are examples of projects where owners ended up paying much more than what was needed due to an overtly conservative design. On the other hand, there are other projects where the thorough geotechnical investigation lowered the perceived risk and allowed the owner/designer to allocate funds more effectively. A good quality investigation can lead to cost-effective solutions such as ground improvement. Solutions like this need a quality engineering assessment, and a proper engineering assessment needs reliable information.
Allocation of the geotechnical risk is another tool in risk management. However, some owners do not have a realistic expectation of the concept. Increasingly owners are attempting to download all of the risks onto the contractors without truly understanding the consequences and reliability of this approach.
Contractors should always take the time to price out the risk properly. Even in an ideal scenario, with adequate subsurface information available to the contractors and plenty of time to properly analyze the information, contractors often end up assessing the risk and then price it in their bid. Competitive bidding does not necessarily result in a lower bid or full transfer of the risk. Without proper investigation and a short bidding period, there will always be a limited understanding of the scope of the risk by the contractor. The contractor will either 1) accept the risk by throwing money at it, 2) ignore the risk and claim later or 3) refuse to bid due to unacceptable risks.
The balance of court decisions dealing with changed soil conditions demonstrates that site investigation clauses in contracts are not always upheld. The majority of changed soil condition cases are settled without going to court and owners eventually pay a penalty. Among the cases that go to court, the success rate for owners is around 40 per cent.
In conclusion, geotechnical risk can certainly be minimized, shared, transferred or accepted, but it cannot be ignored or ever eliminated. Each and every project is unique and requires specific planning for a cost-effective and thorough geotechnical investigation, coupled with background research on the site and surrounding area.
Scale or cost of the investigation are not the only issues in determining the effectiveness of a geotechnical investigation. The best way for the owner to manage geotechnical risk is to retain only the most qualified geotechnical firms to provide quality early pre-bid data. Quality of geotechnical data is influenced by procurement method for geotechnical services, which significantly affects risks in construction and overall project cost. It has been proven that going the cheap route when it comes to geotechnical investigation services simply costs owners more in the end.
A properly planned multi-phased investigation with a budget from 0.5 per cent to 2.2 per cent of the project cost is proven by historical evidence to be effective on most projects. It’s also important to build in contingency costs for the effects of phased information unearthing something unforeseen or changes along design development warranting further investigation. Savings in the bid price have been achieved four to 15 times the cost of a thorough and proper geotechnical investigation. Remember, in the end you pay for a site investigation whether you have one or not. If a decent investigation is not conducted, you will pay for it through overly conservative design, construction delays, contractor claims, and of course, lawyers. Eventually litigation costs end up being much higher than the cost of initially hiring competent engineers and conducting a proper geotechnical investigation.
In closing, remember, don’t be afraid of risk, just give projects the due diligence they deserve. When people in all areas of a project work together to mitigate the risks involved, everyone wins.
Masoud Manzari is a senior geotechnical and hydrogeological engineer with over 23 years of experience and has been involved in a wide range of civil engineering projects, specifically for structures built on challenging soil sites.
Mark Tigchelaar is president and founder of GeoSolv Design/Build Inc. Tigchelaar is a licensed engineer in both Ontario and Alberta, chair of the industry Advisory Board of York University, and the past chair of the Canadian Geotechnical Society-Southern Ontario section.