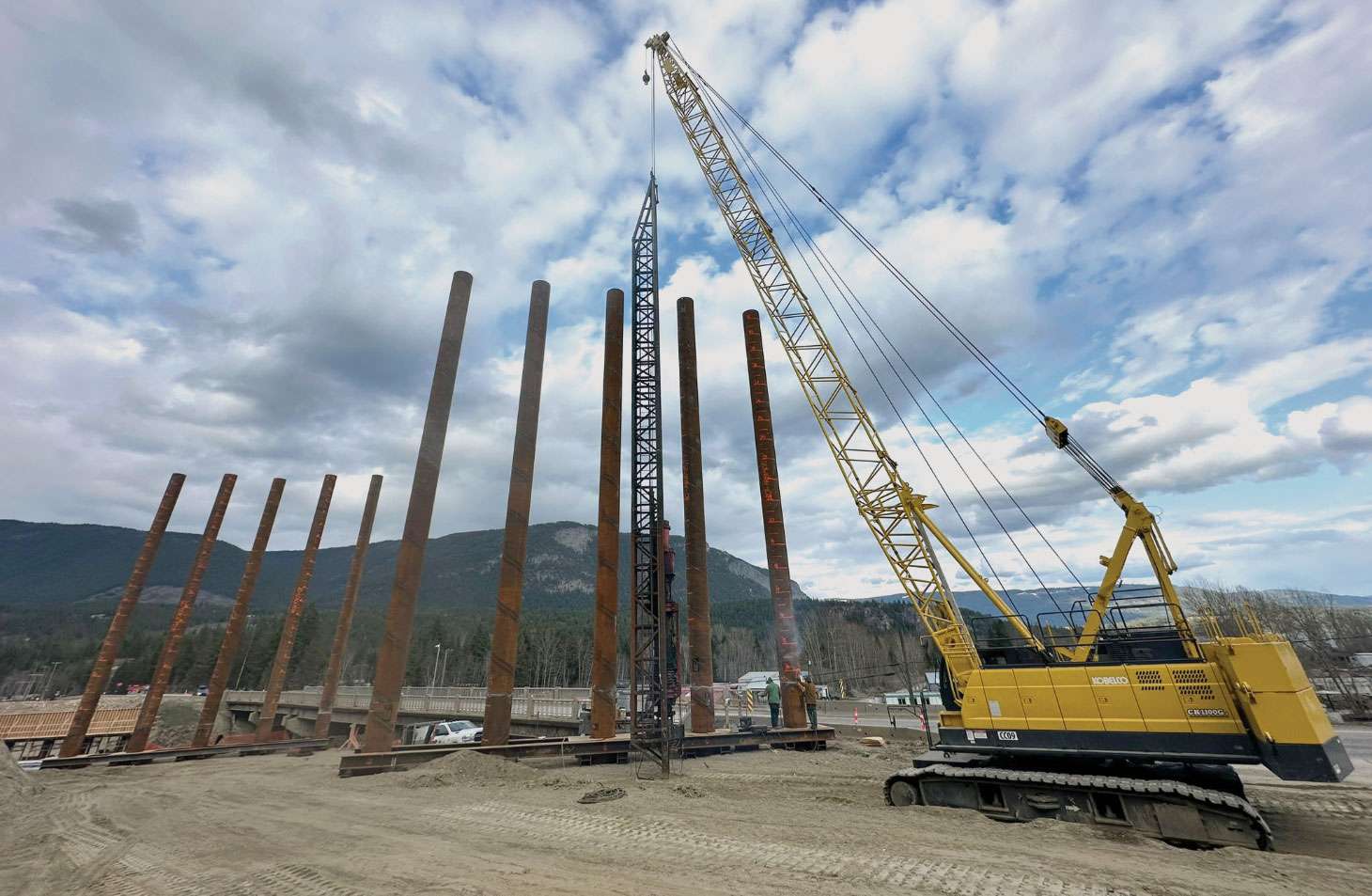
Henry Drilling has always prided itself on its willingness to take on challenging, large-scale projects. One of the Langley, B.C.-based company’s latest undertakings is certainly proof of that.
Henry Drilling is one of several companies involved in upgrades to a 4.3-km section of the Trans-Canada Highway from Ford Road to Tappen Valley Road near Kelowna, B.C.
The $243 million project is funded by the B.C. provincial government and the Government of Canada. Most of the cost ($161 million) will come from the provincial government while the remaining $82 million will be provided by the federal government through the New Building Canada Fund.
The upgrades will include widening the stretch of highway from two lanes to four, replacement of the existing Tappen overhead bridge, construction of a new frontage road system and installation of a median barrier to increase road safety. Work began last October and is scheduled to wrap up by Oct. 31, 2026.
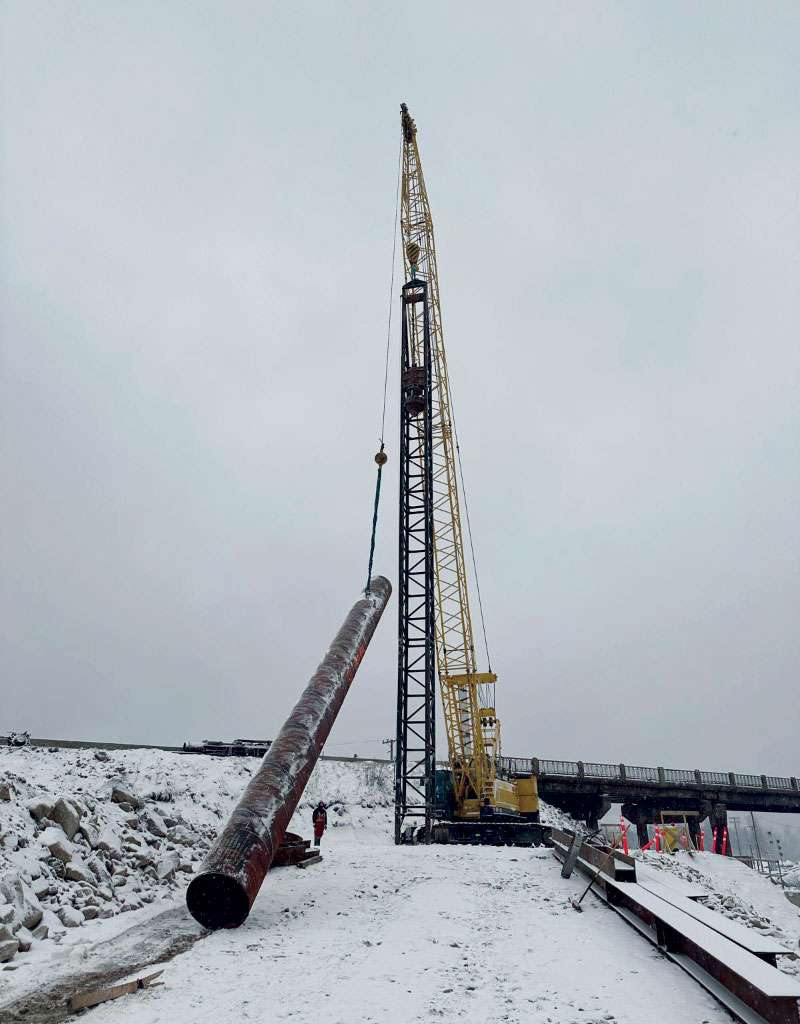
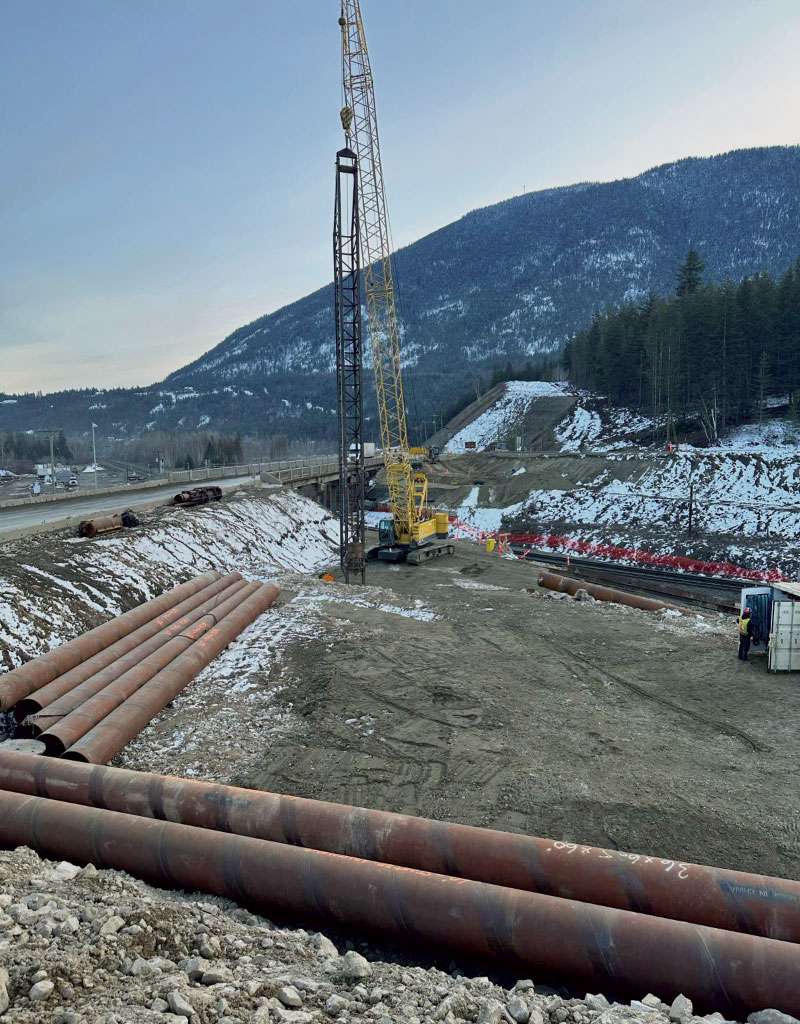
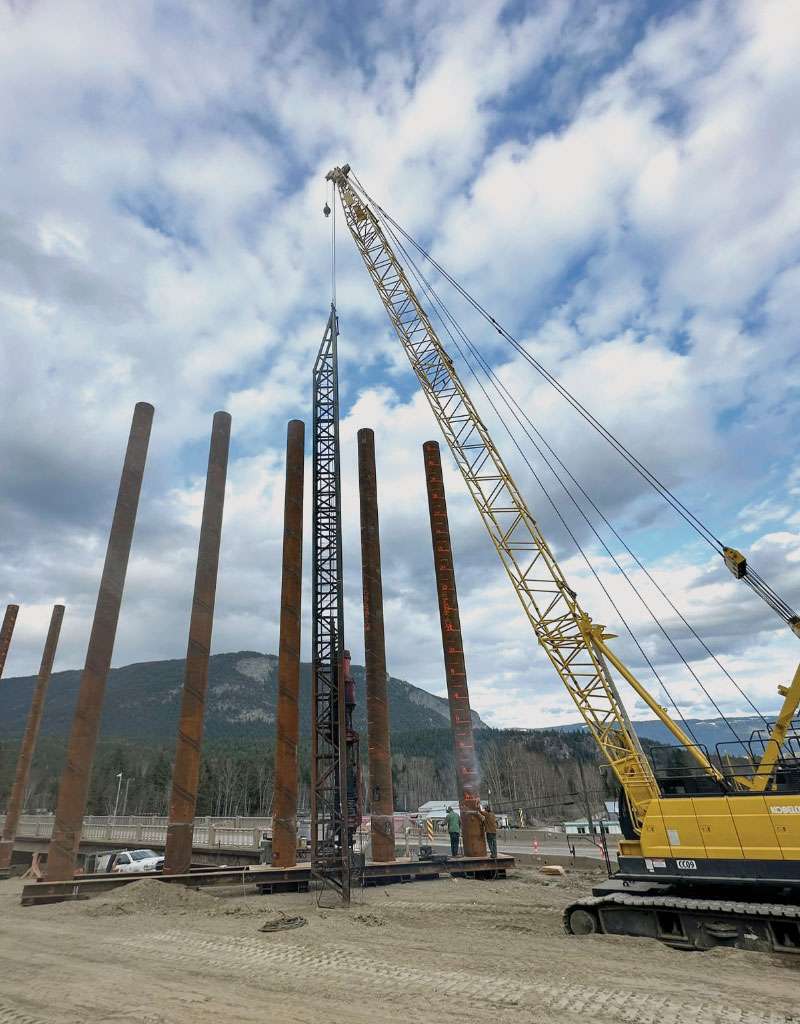
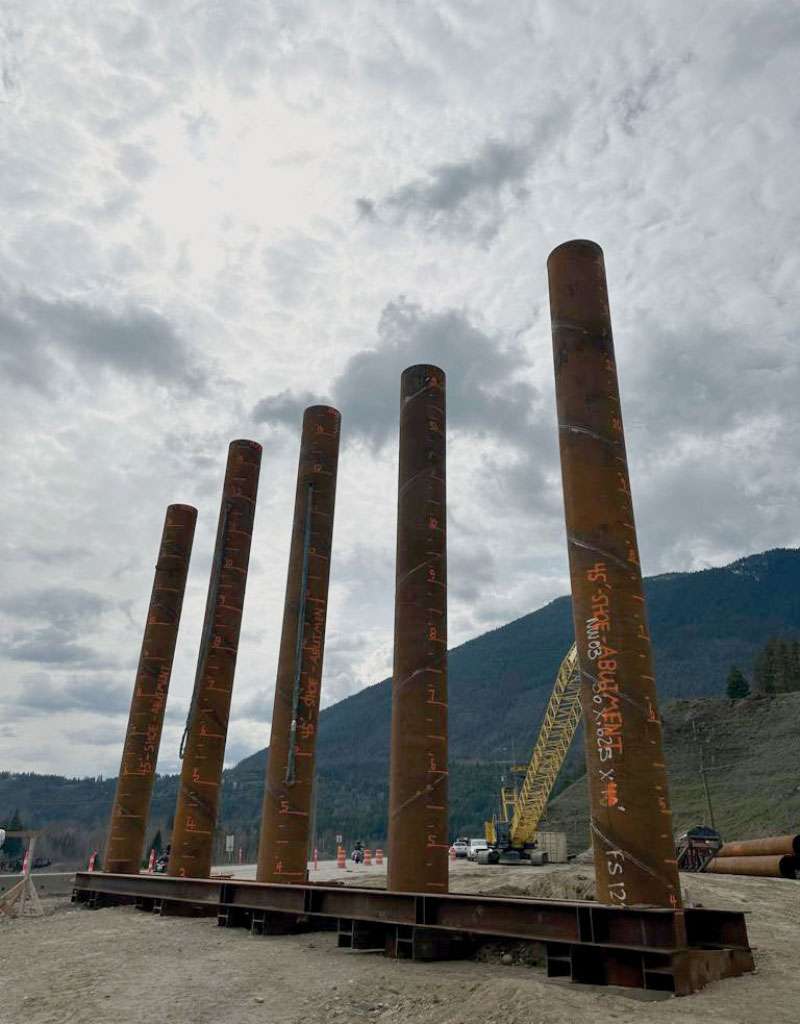
Henry Drilling, which specializes in deep foundation work, is overseeing four components of the massive undertaking. A substantial portion of their efforts will be focused on driving the piles that will be required for the new Tappen Bridge. It will also install piles for a new bridge being built across Tappen Creek, install temporary sheet pile shoring to accommodate the removal of the existing pier caps at the current Tappen bridge, and perform some shoring work to allow for the replacement of a culvert near White Creek.
The decision to replace the aging Tappen overpass was made after it was determined it would have been cost prohibitive to repair the 50-year-old span.
The work Henry Drilling is doing as part of the bridge replacement will be conducted in two phases. The first phase, which wrapped up at the end of April, involved driving a total of 21 steel pipe piles to support the east-bound section of the new span. Each of the piles was 914 millimetres in diameter with 15-mm wall thickness. Each section of pile measured between 30 and 52 metres in length. The second phase, which is slated to begin in 2025, is similar in scope to the first. It will begin following demolition of the existing bridge, which will occur when all work is completed on the east-bound section of the new bridge and it is open to the public.
“You get to know the flaggers and you get to know the train schedule and what’s acceptable and what’s not acceptable.”
Jared Poirier, Henry Drilling
Senior project manager Jared Poirier says during the geotechnical investigations, it was confirmed that there were no subsurface layers dense enough to use end-bearing piles. As a result, the piles being used as part of the bridge replacement had to be designed as friction piles, which rely on the friction between the surface of the pile and the surrounding soil to support the load.
“In terms of the current ground conditions there, it’s a lot of silty sand deposits,” he said. “As a result, the soil itself is kind of dictating why we’re using the methods we’re using. In these types of soft ground conditions, where there are long piles to install, driven pipe piles are the quickest, most cost-effective [option].”
The use of friction piles added some complication to the work on the bridge’s foundation. Once initial driving was complete, the pile capacity did not reach the requirement and as a result, a seven-day wait period was required to allow the piles to set up. This period allowed the excess pore water pressure in the ground to dissipate, increasing soil stress. Following the seven-day wait period, PDA testing was conducted to confirm the piles had achieved capacity.
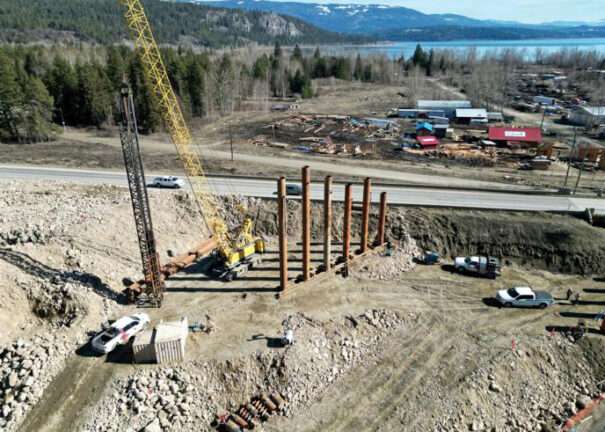
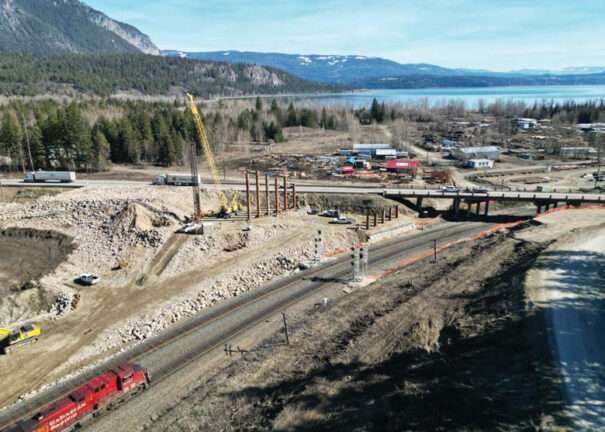
Further complicating matters was the fact that the piles had to be driven about 35 feet from an active CP Rail line. That meant the Henry Drilling crew had to co-ordinate closely with CP flaggers to ensure they held off doing any piling activities during the times trains were passing by.
“You kind of get into the swing of it after a few days. You get to know the flaggers and you get to know the train schedule and what’s acceptable and what’s not acceptable,” said Poirier.
Foreman Anthony Calnan says another detail his crew had to be aware of during pile driving was the fact they were working near the existing highway. That made vibration monitoring necessary as well as more frequent inspections of the equipment and accessories they were using.
A tracked, 110-tonne lattice boom crawler crane was used to drive the piles. Most of the driving was completed with a diesel hammer, although a drop hammer was used as well. All the equipment being used to drive piles for the bridge is owned by Henry Drilling. Since there is no storage facility near the bridge site, equipment had to be brought to the location for each phase and moved to one side of the bridge or the other as needed.
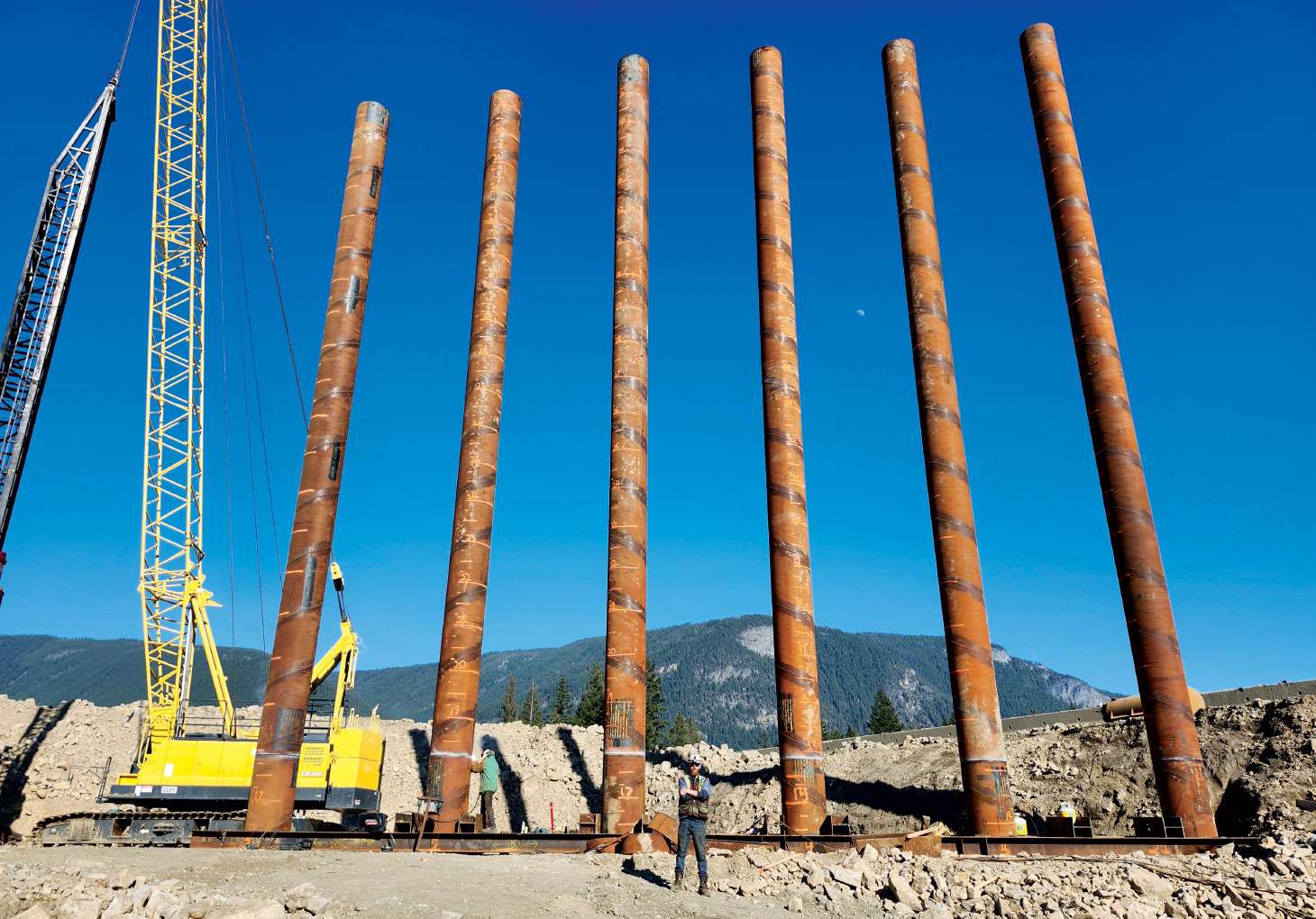
The same holds true for the steel pipe piles, which posed another challenge, since they had to be ordered from overseas before work began to ensure availability. Thankfully, Henry Drilling was able to work out agreements with its supplier to keep the pipe at that company’s storage yard until it was required at the jobsite.
Calnan says the tight footprint of the construction site required careful co-ordination to ensure the piles were unloaded and distributed as quickly and efficiently as possible.
“The biggest issue on any jobsite in terms of things flowing smoothly is how many times you have to handle the material. That means ensuring that the pipe comes off the truck, hits the ground once and the next time you move it, it’s being loaded into the leads to be driven or to be picked off the ground and welded onto the existing pipe and then driven,” he said.
“It’s all about the fewest amount of moves off the truck to [installing] in the ground. If it’s off the truck and then needs to be moved unnecessarily, you’re going to have a very unhappy crew. If it’s off the truck in a single move and a few controlled steps and in the ground, morale’s going to be much better onsite.”
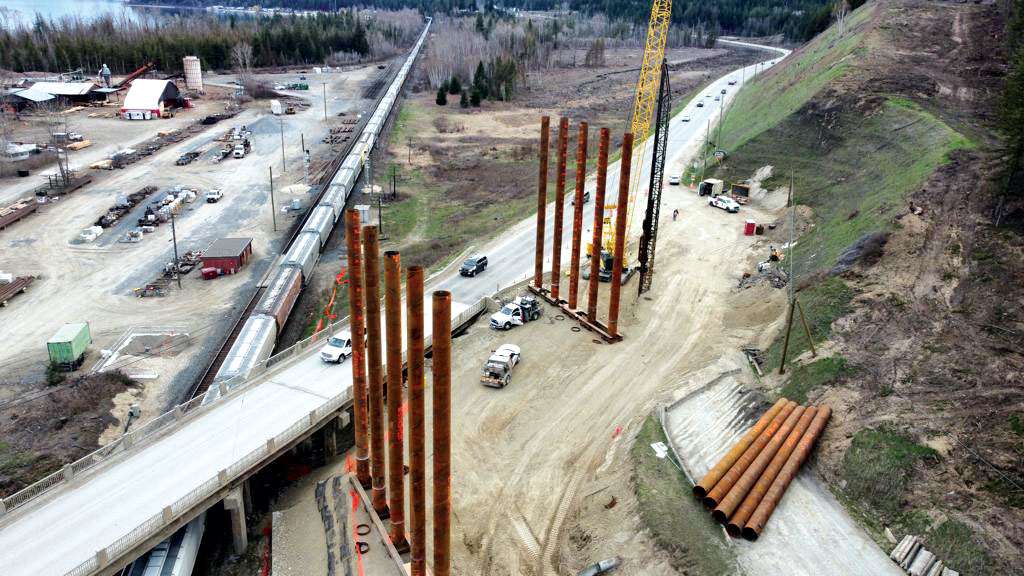
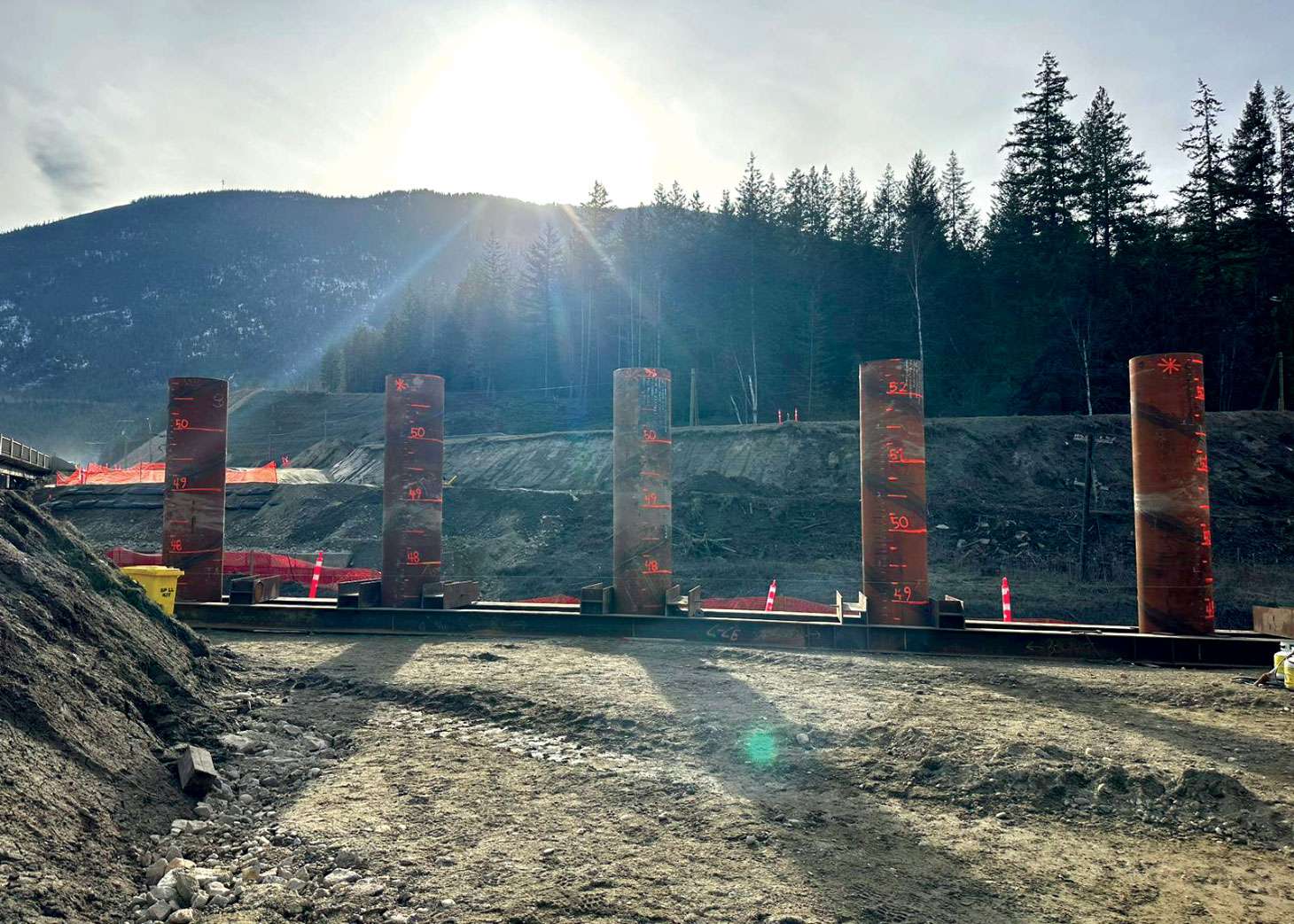
Once work on the new Tappen overhead bridge is completed and it’s open to the public, the old span will be demolished. That will require the existing pile caps at the current site to be removed. At that point, Poirier says his company will be designing and installing a sheet pile shoring system to safely support the nearby rail line while the caps are removed and backfilled.
“The design process for it will be in-depth. There’s a bit of red tape to go through and it has to go through multiple levels of review because the rail infrastructure is critical,” he said.
Poirier says the only environmental concern his company has had to deal with during its work on the new bridge has been noise related. Henry Drilling originally planned to run a Monday-to-Sunday schedule but had to scale that back to six days a week because of local noise restriction bylaws that don’t allow any pile driving on Sundays.
While the Tappen Creek Bridge will be much smaller in scale than the overhead bridge, Poirier says it will involve similar methodology. A total of 18 steel pipe piles will be driven into the ground to provide support. Each pile will measure 610 millimetres in diameter with a 15.9-mm wall and will be driven to a depth of approximately 34 metres. They will be designed as friction piles because the soil near the smaller bridge is similar to that near the base of its larger counterpart. That work is scheduled to begin in 2025.
The final aspect of Henry Drilling’s involvement in the highway upgrades project is the installation of sheet piling at White Creek. This design-build will allow the existing culvert to be removed and facilitate excavation and additional pre-load during the installation of the new one, says project co-ordinator Cesar J. Sheen.
“The biggest issue on any jobsite in terms of things flowing smoothly is how many times you have to handle the material…. If it’s off the truck and then needs to be moved unnecessarily, you’re going to have a very unhappy crew. If it’s off the truck in a single move and a few controlled steps and in the ground, morale’s going to be much better onsite.”
Anthony Calnan, Henry Drilling
Calnan says what he is most proud of in terms of his company’s contribution to the project is how it has met all the scheduling requirements set out by contractor Emil Anderson Construction in a timely manner.
“I think it was an aggressive schedule from the beginning. The fact that we got in there and had minimal hiccups that were managed accordingly, and we got out of there quickly was a big win for us … and for Emil Anderson and the ministry team,” said Calnan. “That was important for us, but that also makes a big difference to everybody involved. The last thing these guys want to be doing is pouring bridge decks and structure works in the winter.”
Calnan says much of the credit for that work being performed in a timely fashion belongs to the crew on site. Many of them have been involved in similar efforts for the company in the recent past, including projects such as the construction of three climate-resilient bridges along the Coquihalla Highway, a bridge replacement along Highway 1 near Falls Creek and another one near Tank Hill.
“I think we have an outstanding group of guys out there. My hat goes off to the crew,” said Calnan. “I don’t think we could have done nearly what we did without the guys we had on the ground.”
“It looks simple but it’s not,” Sheen added. “It’s a great effort that all our guys put in to make it happen. If we don’t have that synergy, it doesn’t work.”