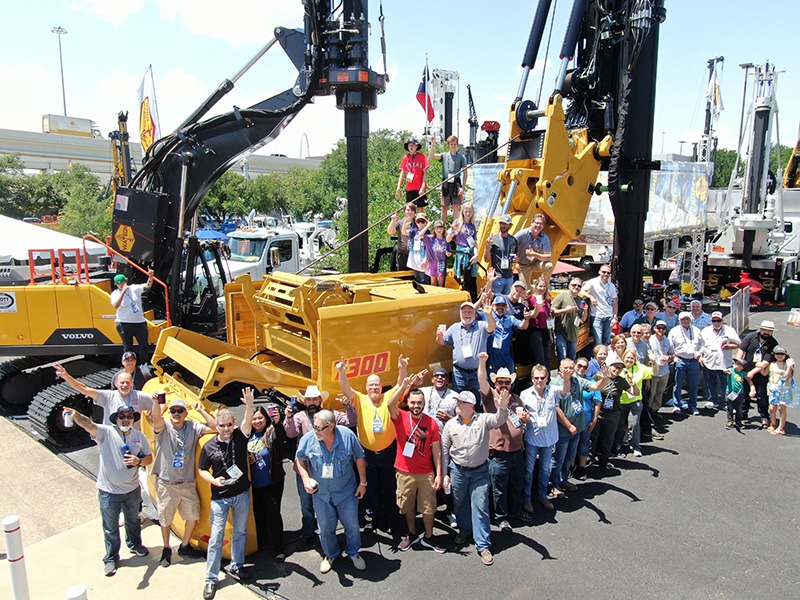
Watson Drill Rigs took root a century ago in Fort Worth, Texas, when Verne Watson rigged up a single flatbed truck and started the Fort Worth House Moving Company in his hometown. From the start, it was both contractor and manufacturer, adapting equipment to meet the needs of customers with versatility and willingness to innovate that would come to define the business, and quickly grew to include larger structures and industrial machinery.
Watson first set steel girders to support a bridge over the Colorado River for the Texas Department of Transportation, using the newer system of drilled and cast foundations. Reinforced concrete shafts proved to be perfect foundations for the geology of Texas and beyond, and soon, the Watsons were installing them routinely.
The first Watson drill rig, developed in 1940, is the stuff of company legend. Their history states “they attached an engine and transmission from an old Buick to the bed of a pole truck, used a modified rear truck differential as a rotary and stabbed an oilfield Kelly bar through the middle.”
“We had two or three competitors – now [there are] dozens of drill manufacturers,” said Doug Watson.
Since then, many manufacturers have adopted Watson-introduced innovations such as short mast and rathole rigs for powerline and under-bridge work. Even the Trevi Group used the Watson 5000 for inspiration on their first crane attachment design nearly 50 years ago, says Doug. The company now holds over a dozen patents, three of which were awarded to Doug.
As the equipment became more complex, the manufacturing and contracting sides of the company became more distinct. By the mid-1950s the company was known as Watson Foundation Company and had operations in Denver, Colo., Atlanta, Ga., and Fort Worth. It mostly drilled shaft (bored pile) contracting along with the manufacturing of equipment and tooling to meet the company’s own needs. By the early 1960s, as equipment sales to other drilling contractors began, Watson shifted to become primarily a manufacturer, now called Watson Manufacturing Company. By 1965, it was selling rigs into countries beyond the U.S., and in 1968, David, Verne’s grandson and the current president of the company, joined the family business full time, and Watson Drill Rigs delivered its first “mobile” rigs to Canada. Today, Watson Drill Rigs is a four-generation family company.
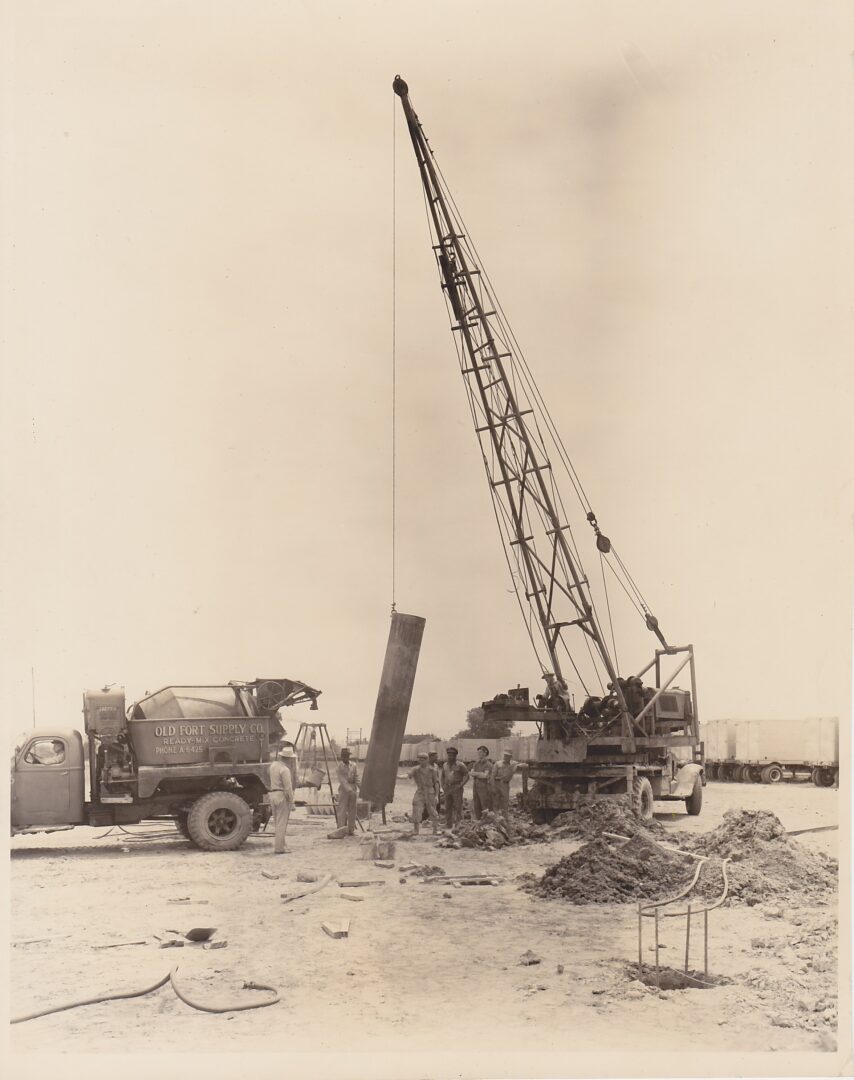
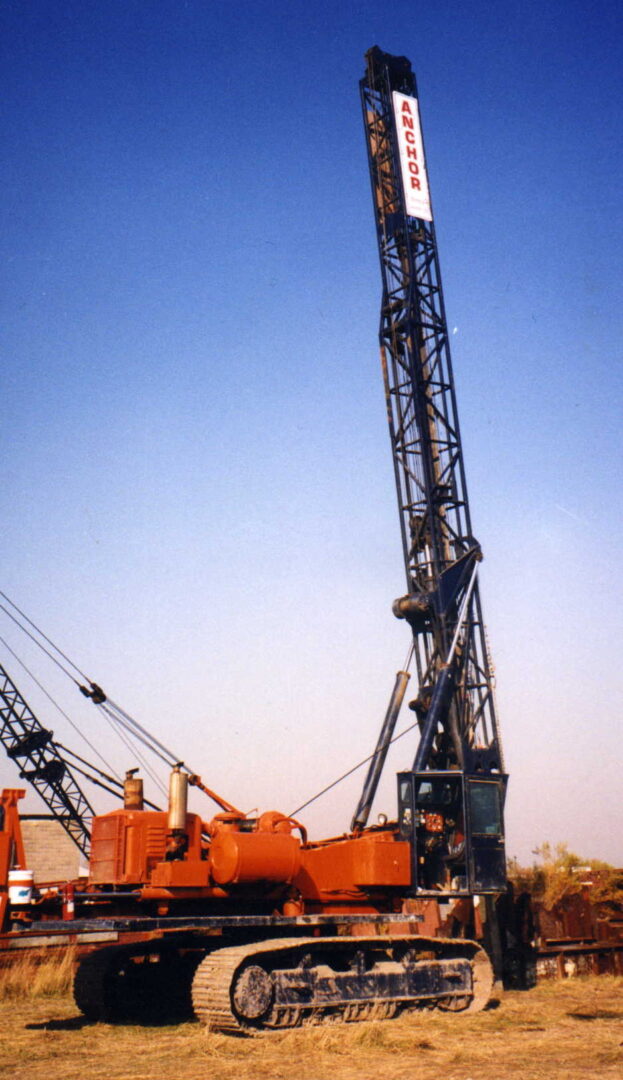
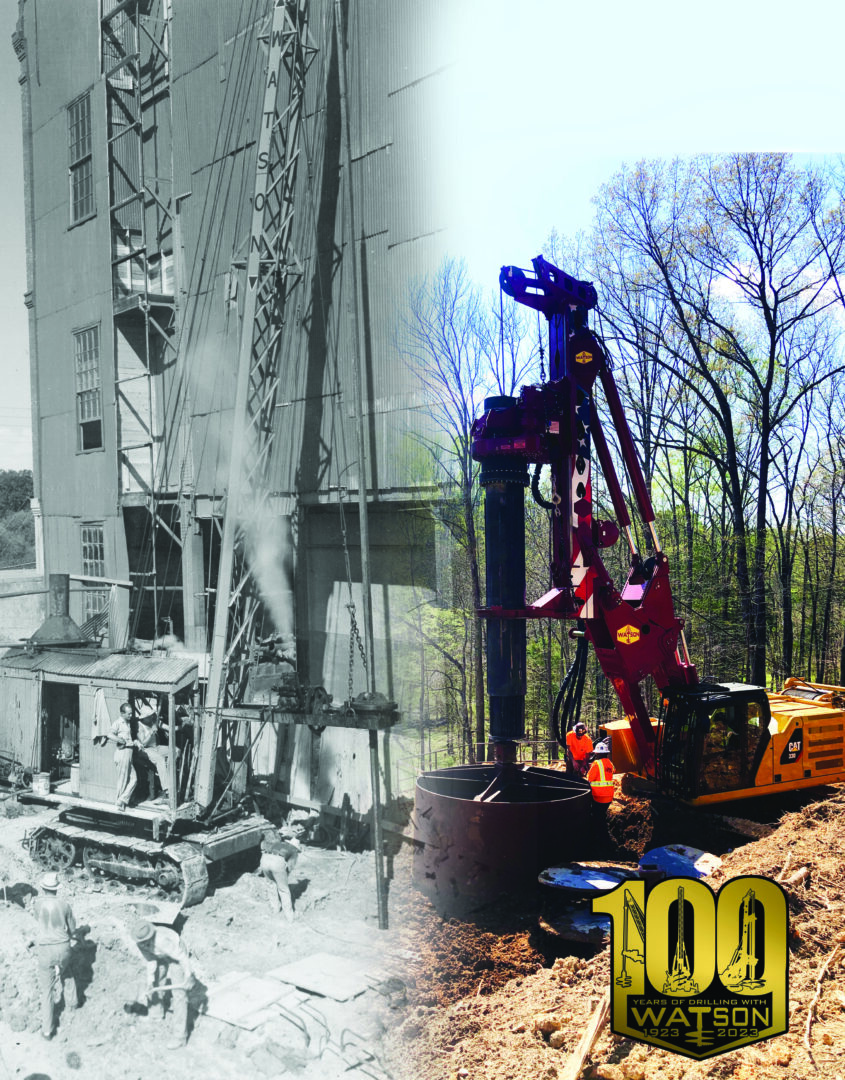
A reputation built on tougher rigs
Doug, David’s son, returned to work at Watson in 2002 after obtaining a graduate degree in mechanical engineering at the University of Texas. Today the company’s CEO, he introduced his innovative American take on a European-style drill rig, the Model 4400, in 2004, incorporating newer manufacturing and drilling methods while preserving the quality that made Watson’s rigs so successful over the previous decades.
“Foundation drilling is one of the most demanding applications for construction equipment, and our reputation has been built upon tougher rigs,” Doug said.
These rigs are designed to take the punishment of drilling large-diameter holes in North America’s shallow rocks, built rugged to provide years of field performance and to maintain a high resale value. Since late 2019, when the Watson family regained full ownership of the company from Soilmec, a decade after becoming part of the Trevi Group of companies, things are going well.
“Our production capacity is full, we’re expanding product lines and developing new machines,” Doug said.
He and his father maintained management control during the decade-long Trevi years.
“From that perspective, not much changed, but the opportunity to be 100 per cent family and American-owned again was a no-brainer,” Doug said. “Now, rather than serving shareholders, we can make decisions based upon the long-term health of our company, pursue what we think the market needs from us. We try to get out there and listen to what customers are asking for – that’s been characteristic of our company for a long time.”
In the 60-plus years since Watson first manufactured rigs specifically to sell to other contractors, it has produced more than 1,500 of them, says Doug.
“If you divide by 100, it doesn’t seem that impressive, but most of them have been in the last few decades.”
Surprisingly, a considerable number of those rigs are still in use.
“We’ve got lots of machines that are 40 years old, and a refurb program where people bring in 30-year-old machines – we’ll fix them up and rewire and replumb them, and they go on another 20, 30 years.”
Ninety-five per cent have been sold in the U.S. and Canada, says Doug, for use in the foundation, energy, utility and earth retention industries. Canadian customers have included Ontario Hydro, which bought a prototype in 1967, and Anchor Shoring, now part of Green Infrastructure Partners, which used its first Watson rig in 1987.
Unlike high-volume production manufacturers selling their machines through dealers, Watson is a direct-to-customer equipment manufacturer, with all manufacturing done in America and all assembly done by Watson employees in Fort Worth.
“So we allow customization and modifications to our designs that our customers need to solve their problems. We can talk directly to the customer, we can hear [their] issues, we can follow up – that feedback loop is quick,” Doug said.
Celebrating a century of grit and innovation
Watson Drill Rigs’ centennial celebration in April was another opportunity for the Watson team to demonstrate appreciation for its customers. The three-day event was attended by hundreds of people and featured product presentations, factory tours, drilling demonstrations with hands-on drill training sessions, Watson’s annual rig wellness inspection program, rig refurbishments and plenty of food, drinks and opportunities for socializing that included golf, clay target shooting, a mechanical bull and live music.
Friday afternoon featured a rotating panel of drilling contractors who shared their companies’ own often-multi-generational histories, how they’d grown over the decades as drilling equipment evolved from steam power to high-pressure hydraulic systems and how Watson drills had contributed to their successes. This session was recorded and the video is available on Watson’s Facebook page at www.facebook.com/watsonusa.
During the height of the pandemic, the company avoided layoffs and kept all 88 employees – almost a third of Watson’s workforce has been with them for over 15 years. In celebrating its history, Watson gave special recognition to those who’ve worked for the company for more than two decades, including two employees who have worked there for more than 50 years.
After an afternoon “hat-hanging ceremony” at the historic White Elephant Saloon for David, whose cowboy hat takes its place among those of eminent locals honoured for their contributions to the community, the celebration culminated with a rooftop gathering at the Marriott Hotel restaurant overlooking Fort Worth’s historic stockyards.
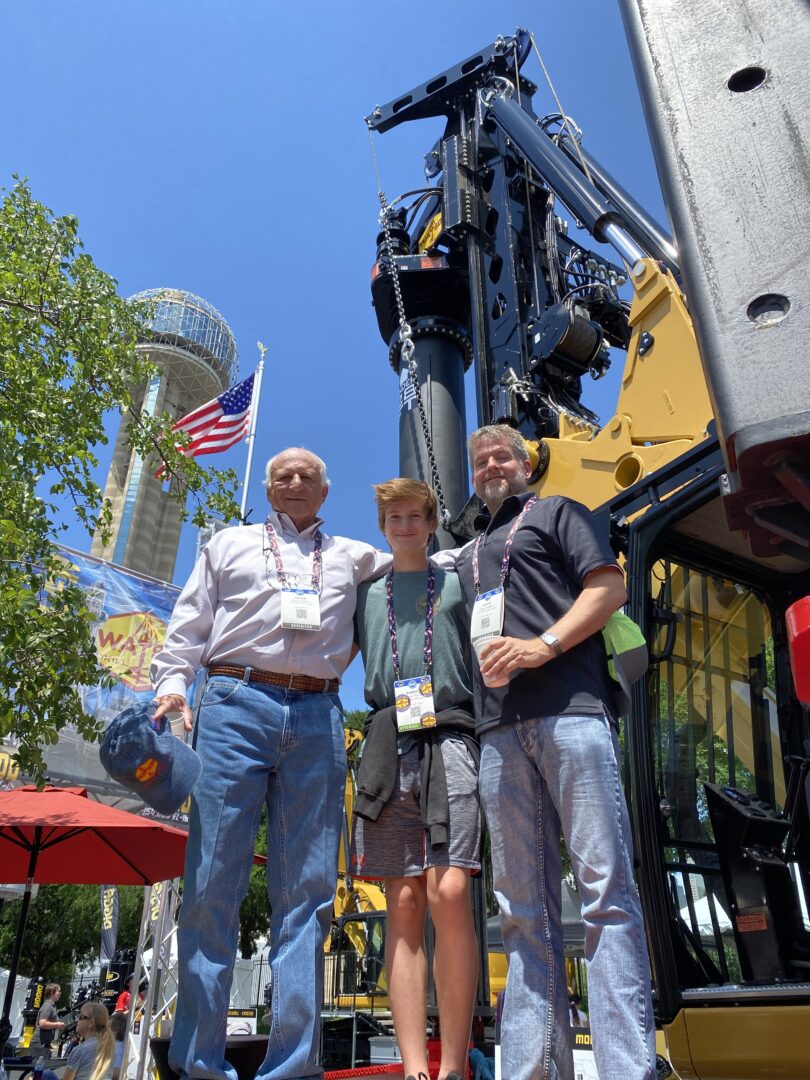
‘Hydraulic pilot-operated systems are very proven’
“Frankly, [there are] half a dozen things that people really use to drill a hole – the rest of it is kind of gadgets and marketing,” Doug said.
While many of its newer models leverage advanced electronics, and Watson has long included electronic features such as depth counters and level indicators, putting computer control in the way of actually drilling the hole is risky, he says.
“There’s a lot of pushout in the construction world for the latest and greatest, electric-driven, battery-powered, all kinds of new technologies, but electronics are still a frustration point with [drilling] rigs. They’re harder to diagnose and harder to fix, and if the computer system has a short or a broken wire anywhere, you could potentially lose the ability to drill,” he said.
“Hydraulic pilot-operated systems are very proven. So we try to improve upon the fundamentals of the machines – the rotary designs, the Kelly designs, the things that actually make you money. We don’t like to put a bunch of candy on the machines that can break, just focus on the things that are important, like speed, durability and lack of downtime. I still think that good, talented operators are key to having productive machines.
“Humans are great [at] dealing with the unexpected, computers are great [at] dealing with predictable things – and drilling is by no means predictable.”
Photos courtesy of Watson Drill Rigs