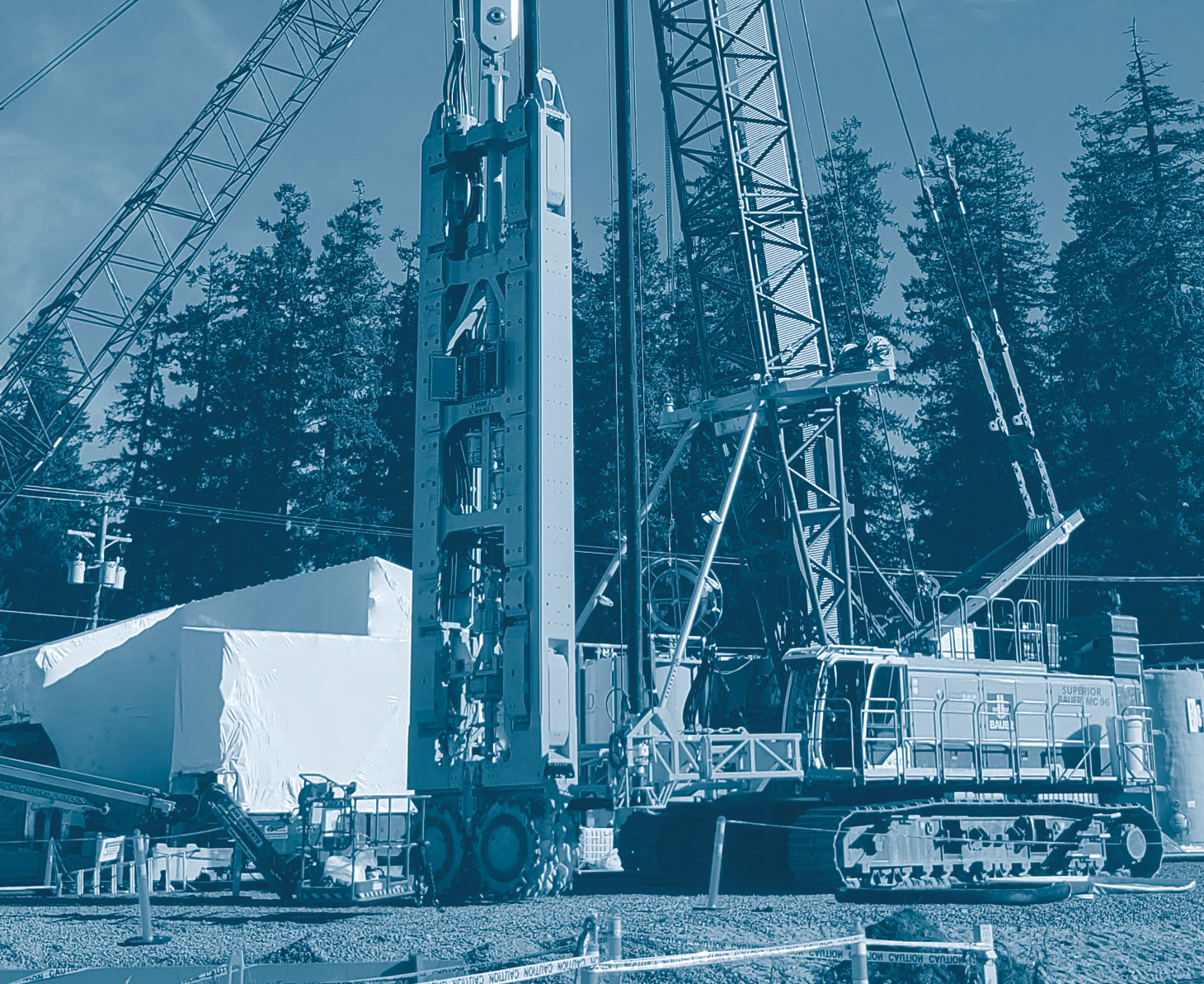
A Canadian deep foundations construction firm that played an important role in ongoing seismic upgrades to the John Hart Dam on Vancouver Island’s Campbell River says teamwork was key to its efforts to help fortify the massive structure and bring it up to modern-day standards.
Bauer Foundations Canada, a subsidiary of German-based Bauer Spezialtiefbau, was involved in two important aspects of the project, which is expected to cost between $646 million and $923 million, and be completed by 2030.
The first was ground improvements on the north earthfill dam. That included building earth-filled berms upstream and downstream from the dam. As part of that work, Bauer crews had to use a cylindrical, electrically-driven probe called a vibroflot to install stone piles, or columns, into the earthen structure to help solidify the soil and increase its density in the event of an earthquake.
The other aspect was the addition of a low-permeability plastic concrete cutoff wall within the middle earthfill dam that will act as the new primary seepage barrier. The cast-in-place plastic concrete cutoff wall runs parallel to the existing seepage barriers of the dam (250 metres) and extends from the very top of the dam all the way down to bedrock or the lower grey silt layer (up to 38.5 metres).
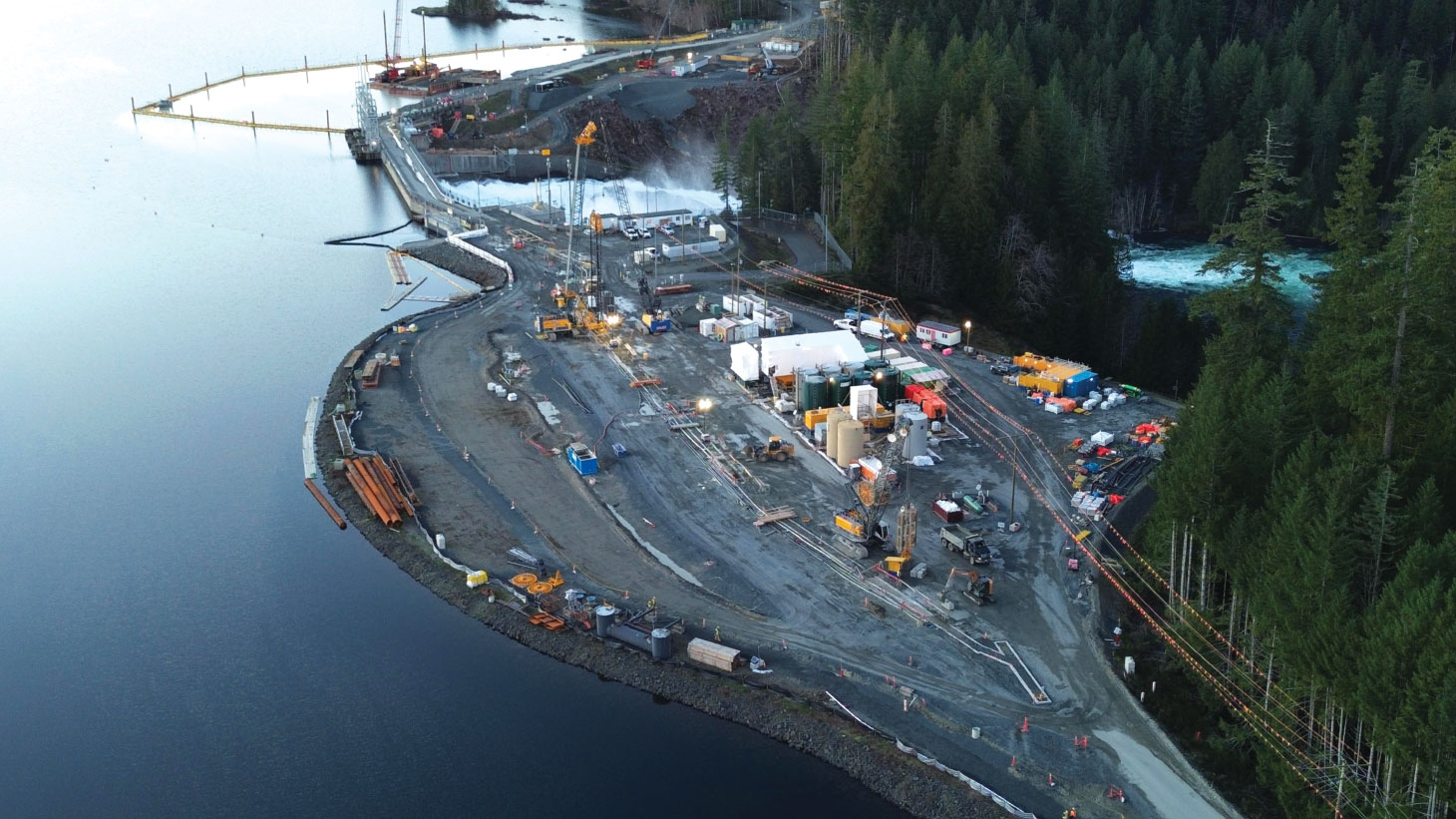
The purpose of the new primary seepage barrier is to improve seismic performance, reduce groundwater seepage through the middle earthfill dam from an adjacent reservoir and provide protection to the people of Campbell River, which is located on the floodplain of the reservoir. When work is completed, the dam is projected to withstand a one-in-10,000-year event such as a severe earthquake of a magnitude of 9.0 or stronger.
The John Hart Dam was built in 1947 on Vancouver Island, one of the most seismically active zones in British Columbia. The current work follows a six-year, $10 million study that looked into what could be done to prepare dams in the province for a major seismic event.
Bauer senior project manager Jeff Pattison says while his company has been involved in similar projects in other countries, this was the first time it undertook one of this nature and magnitude in Canada.
One of the biggest challenges associated with the project was the need to bring on people with experience in the specialized techniques required to do the work involved. As a result, Bauer brought in experienced workers from as far away as France, Italy, the U.S., Malaysia, Indonesia and its headquarters in Germany to augment and train the people it already had on the ground in Canada.
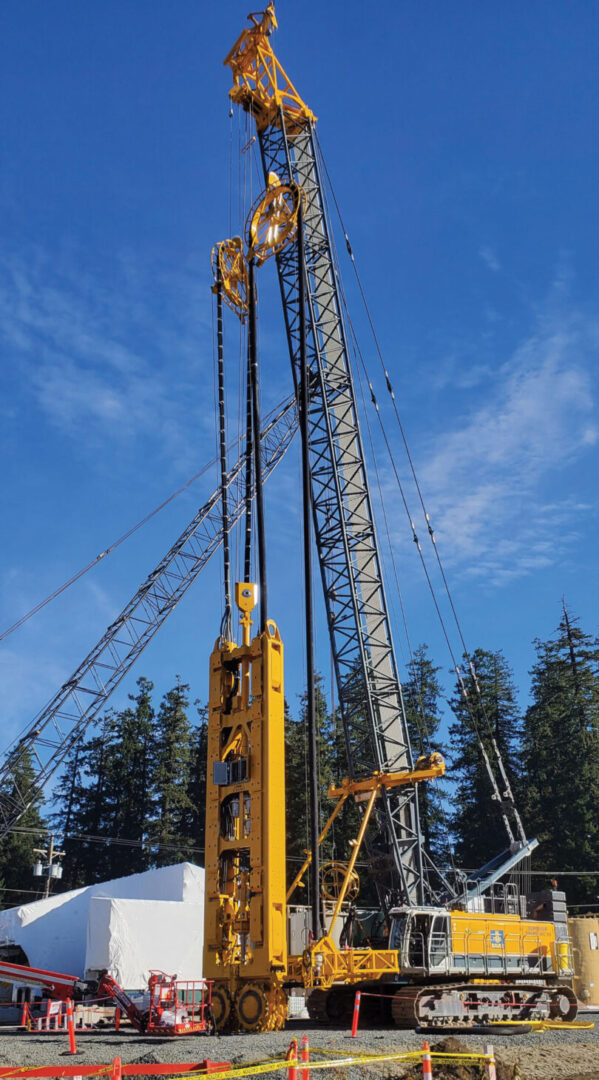
“We brought in experts from around the world, from at least half a dozen countries. As well, we brought in people from six provinces in Canada and trained them. It was a great success on that front. It was just a great experience all around,” said Pattison. “Having that experience to call on was extremely valuable. Not only did it give us the confidence to do it, but we could really focus our efforts with the experience they provided.”
Part of what made the ground improvements on the north earthfill dam so challenging was the fact that it involved working in marine and land environments. Also, as it’s such an ecologically sensitive area, the project team had to install temporary driven piles into the ground to build a silt curtain that was anchored at the bottom of the reservoir. The curtain helped keep agitated water near the berms from flowing into the reservoir or river and causing any kind of “adverse environmental effects,” says Pattison.
Perhaps the most interesting aspect of Bauer’s involvement in the project was the installation of the low permeability plastic concrete cutoff wall installed within the middle earthfill dam. Think of a giant sheet pile placed within the barrier to prevent water from the nearby reservoir from seeping through the dam.
“We brought in experts from around the world, from at least half a dozen countries. As well, we brought in people from six provinces in Canada and trained them. It was a great success on that front.”
Jeff Pattison, Bauer Foundations Canada
What makes the cutoff wall unique is that it required the use of a unique type of plastic concrete. Pattison says plastic concrete is ideal for such a job because its low permeability and low compressive strength provide the high level of ductility, or flexibility, which is essential in the event of a seismic occurrence.
As part of its preparations, Bauer conducted a series of laboratory trials to test the plastic concrete and ensure it met the necessary strength, permeability and ductility requirements. It began working on the ground improvements and cutoff wall simultaneously in October 2023 and completed its work this past July.
While Bauer has done similar work in several countries, this was the first time it did this in Canada. As a result, the company relied on its international services division to assist in pre-planning and trial mixing with Aecon/EBC General Partnership, the primary contractor. That included performing one of the laboratory trials at its headquarters in Germany because of its experience with performing the highly specialized work. The company also brought in a materials expert from Germany on two different occasions to lend some first-hand expertise to the project.
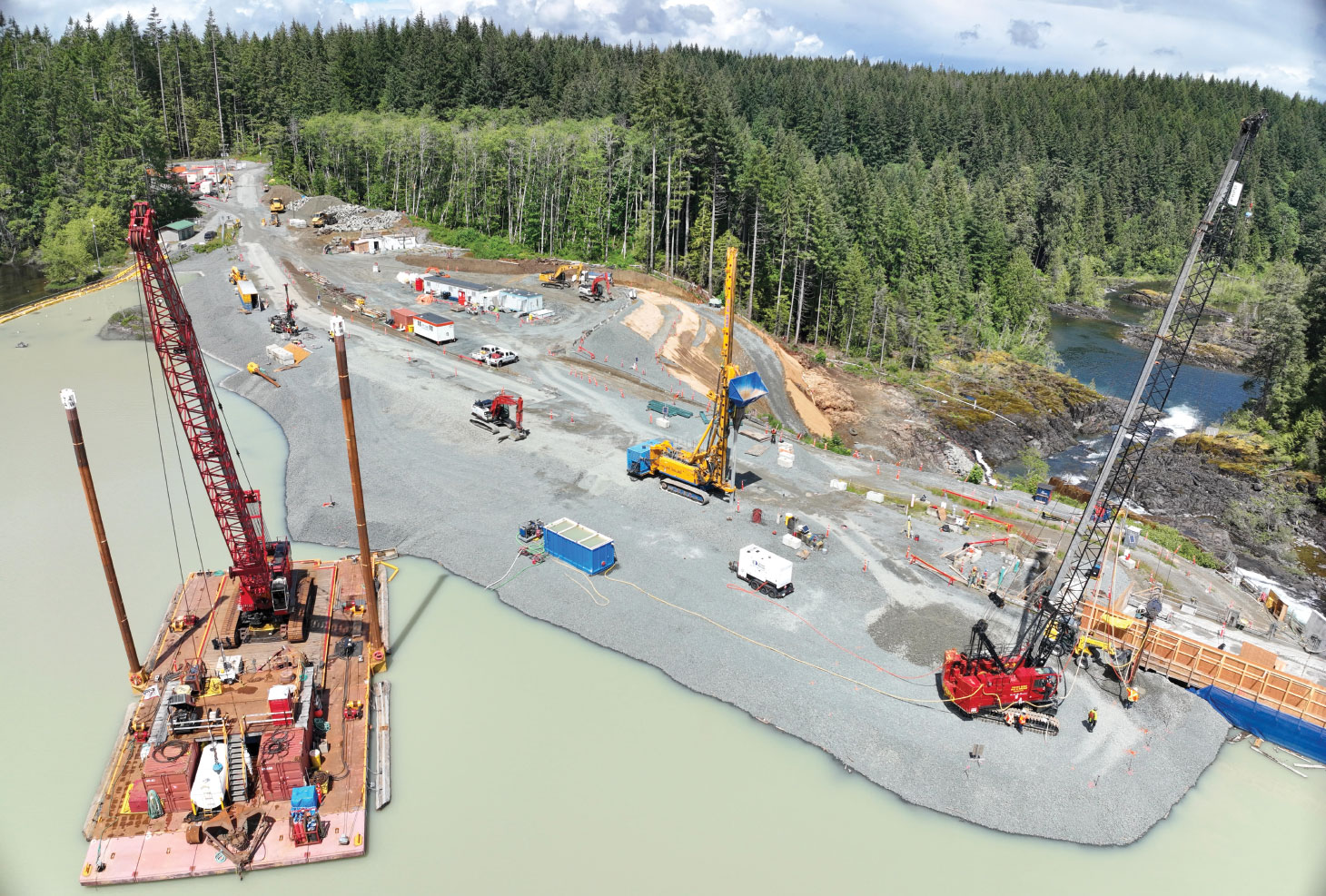
Installing the cutoff wall within the dam also posed a logistical challenge. At any given time, there were as many as 50 Bauer employees working on top of the dam and dozens of pieces of equipment were in play, meaning all of those pieces had to be carefully co-ordinated at all times. “It was basically a one-way street for co-ordinating daily logistics,” Pattison said.
“We had to build our facilities around workable areas. We had to move our equipment, leapfrog it back and forth. The logistics involved in working in such a tight project space was a real challenge. We just had to use the real estate we had. Sometimes we had to stack equipment on top of each other, and other times, we had to build some areas where we would park equipment to allow others to pass.”
Pattison says Bauer employees deserve a lot of credit for the company’s successful completion of its part on the dam project. Two crews worked 12-hour shifts each day, which meant one crew was present throughout the day and then relieved by a second crew in the evening. That required constant communication between the crews and supervisors.
Although winter temperatures never dropped much below -15°C during work on the project, Pattison says the cooler weather did complicate things. “It doesn’t get that cold there, certainly not as much as (in other parts of the country). But we had to take all sorts of measures to keep some of the components of the concrete warm, as well as the equipment, or it would freeze,” he said.
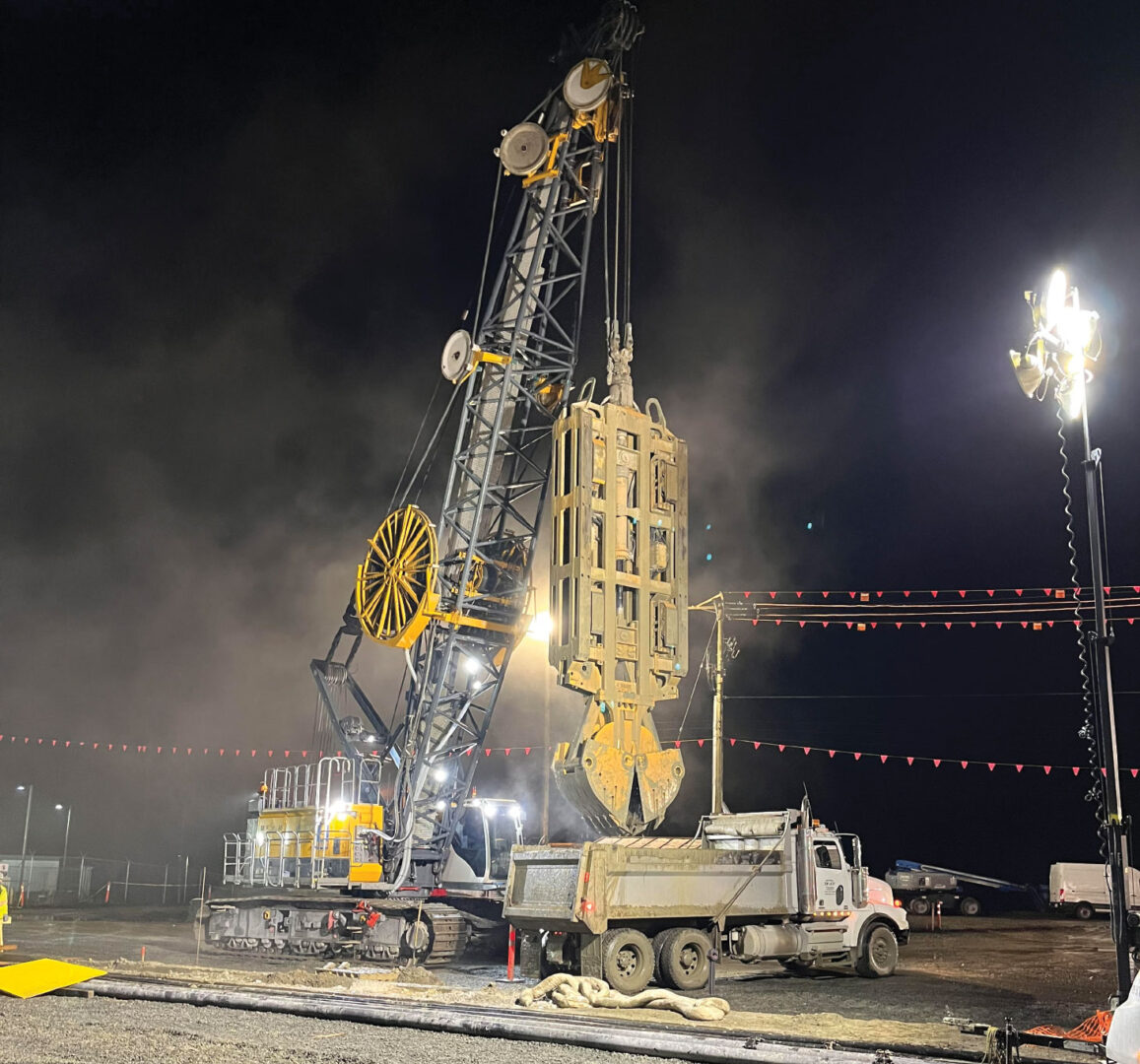
As the area near the dam is so ecologically sensitive, Bauer and the other companies involved in the project undertook a number of measures to ensure they were minimizing any environmental impact. That included using hundreds of active monitoring stations across the dam to track any vibrations or settlement disruptions. There was also a continuous collection of data and monitoring the groundwater level.
Pattison says his company also had to be very diligent about the use of bentonite, a highly absorbent and viscous plastic clay that is used as a binding and sealing agent. Bentonite has a higher pH value than the reservoir water, meaning it is more acidic and could cause major environmental concerns if it were to seep into the reservoir or nearby river.
Bentonite was used to create a slurry to help maintain open trenches along the cutoff wall. As a result, Bauer had to be very diligent about delineating the threat it posed to workers and ensuring only essential equipment and trained people got close to where it was being used.