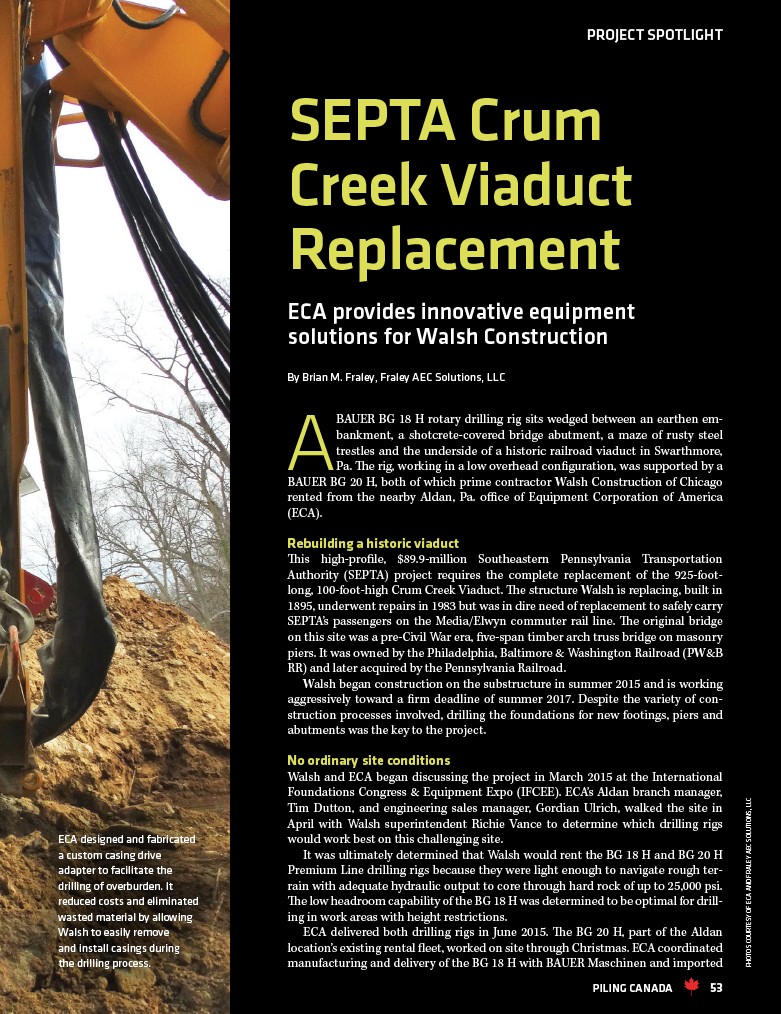
PROJECT SPOTLIGHT
SEPTA Crum
Creek Viaduct
Replacement
ECA provides innovative equipment
solutions for Walsh Construction
By Brian M. Fraley, Fraley AEC Solutions, LLC
A BAUER BG 18 H rotary drilling rig sits wedged between an earthen embankment,
a shotcrete-covered bridge abutment, a maze of rusty steel
trestles and the underside of a historic railroad viaduct in Swarthmore,
Pa. The rig, working in a low overhead configuration, was supported by a
BAUER BG 20 H, both of which prime contractor Walsh Construction of Chicago
rented from the nearby Aldan, Pa. office of Equipment Corporation of America
(ECA).
Rebuilding a historic viaduct
This high-profile, $89.9-million Southeastern Pennsylvania Transportation
Authority (SEPTA) project requires the complete replacement of the 925-footlong,
100-foot-high Crum Creek Viaduct. The structure Walsh is replacing, built in
1895, underwent repairs in 1983 but was in dire need of replacement to safely carry
SEPTA’s passengers on the Media/Elwyn commuter rail line. The original bridge
on this site was a pre-Civil War era, five-span timber arch truss bridge on masonry
piers. It was owned by the Philadelphia, Baltimore & Washington Railroad (PW&B
RR) and later acquired by the Pennsylvania Railroad.
Walsh began construction on the substructure in summer 2015 and is working
aggressively toward a firm deadline of summer 2017. Despite the variety of construction
processes involved, drilling the foundations for new footings, piers and
abutments was the key to the project.
No ordinary site conditions
Walsh and ECA began discussing the project in March 2015 at the International
Foundations Congress & Equipment Expo (IFCEE). ECA’s Aldan branch manager,
Tim Dutton, and engineering sales manager, Gordian Ulrich, walked the site in
April with Walsh superintendent Richie Vance to determine which drilling rigs
would work best on this challenging site.
It was ultimately determined that Walsh would rent the BG 18 H and BG 20 H
Premium Line drilling rigs because they were light enough to navigate rough terrain
with adequate hydraulic output to core through hard rock of up to 25,000 psi.
The low headroom capability of the BG 18 H was determined to be optimal for drilling
in work areas with height restrictions.
ECA delivered both drilling rigs in June 2015. The BG 20 H, part of the Aldan
location’s existing rental fleet, worked on site through Christmas. ECA coordinated
manufacturing and delivery of the BG 18 H with BAUER Maschinen and imported
PHOTOS COURTESY OF ECA AND FRALEY AEC SOLUTIONS, LLC
ECA designed and fabricated
a custom casing drive
adapter to facilitate the
drilling of overburden. It
reduced costs and eliminated
wasted material by allowing
Walsh to easily remove
and install casings during
the drilling process.
PILING CANADA 53