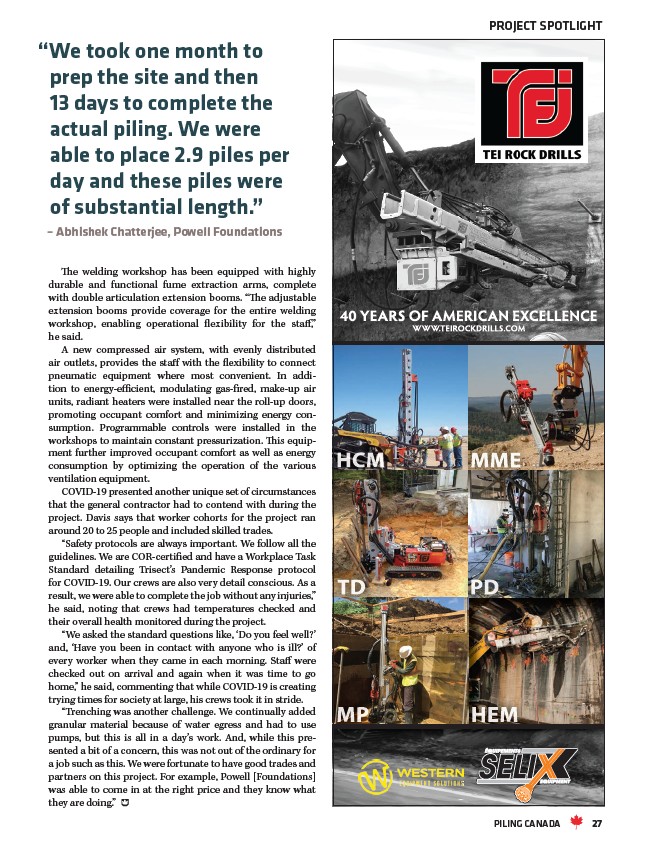
The welding workshop has been equipped with highly
durable and functional fume extraction arms, complete
with double articulation extension booms. “The adjustable
extension booms provide coverage for the entire welding
workshop, enabling operational flexibility for the staff,”
he said.
A new compressed air system, with evenly distributed
air outlets, provides the staff with the flexibility to connect
pneumatic equipment where most convenient. In addition
to energy-efficient, modulating gas-fired, make-up air
units, radiant heaters were installed near the roll-up doors,
promoting occupant comfort and minimizing energy consumption.
Programmable controls were installed in the
workshops to maintain constant pressurization. This equipment
further improved occupant comfort as well as energy
consumption by optimizing the operation of the various
ventilation equipment.
COVID-19 presented another unique set of circumstances
that the general contractor had to contend with during the
project. Davis says that worker cohorts for the project ran
around 20 to 25 people and included skilled trades.
“Safety protocols are always important. We follow all the
guidelines. We are COR-certified and have a Workplace Task
Standard detailing Trisect’s Pandemic Response protocol
for COVID-19. Our crews are also very detail conscious. As a
result, we were able to complete the job without any injuries,”
he said, noting that crews had temperatures checked and
their overall health monitored during the project.
“We asked the standard questions like, ‘Do you feel well?’
and, ‘Have you been in contact with anyone who is ill?’ of
every worker when they came in each morning. Staff were
checked out on arrival and again when it was time to go
home,” he said, commenting that while COVID-19 is creating
trying times for society at large, his crews took it in stride.
“Trenching was another challenge. We continually added
granular material because of water egress and had to use
pumps, but this is all in a day’s work. And, while this presented
a bit of a concern, this was not out of the ordinary for
a job such as this. We were fortunate to have good trades and
partners on this project. For example, Powell Foundations
was able to come in at the right price and they know what
they are doing.”
PROJECT SPOTLIGHT
“We took one month to
prep the site and then
13 days to complete the
actual piling. We were
able to place 2.9 piles per
day and these piles were
of substantial length.”
– Abhishek Chatterjee, Powell Foundations
PILING CANADA 27