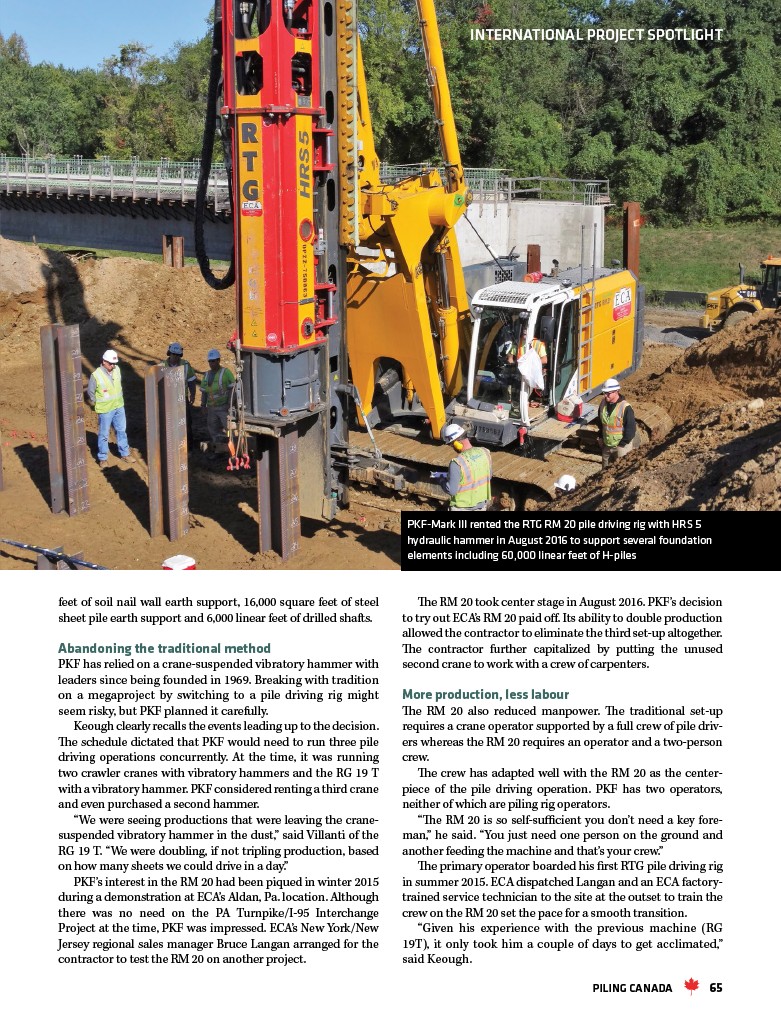
INTERNATIONAL PROJECT SPOTLIGHT
feet of soil nail wall earth support, 16,000 square feet of steel
sheet pile earth support and 6,000 linear feet of drilled shafts.
Abandoning the traditional method
PKF has relied on a crane-suspended vibratory hammer with
leaders since being founded in 1969. Breaking with tradition
on a megaproject by switching to a pile driving rig might
seem risky, but PKF planned it carefully.
Keough clearly recalls the events leading up to the decision.
The schedule dictated that PKF would need to run three pile
driving operations concurrently. At the time, it was running
two crawler cranes with vibratory hammers and the RG 19 T
with a vibratory hammer. PKF considered renting a third crane
and even purchased a second hammer.
“We were seeing productions that were leaving the cranesuspended
vibratory hammer in the dust,” said Villanti of the
RG 19 T. “We were doubling, if not tripling production, based
on how many sheets we could drive in a day.”
PKF’s interest in the RM 20 had been piqued in winter 2015
during a demonstration at ECA’s Aldan, Pa. location. Although
there was no need on the PA Turnpike/I-95 Interchange
Project at the time, PKF was impressed. ECA’s New York/New
Jersey regional sales manager Bruce Langan arranged for the
contractor to test the RM 20 on another project.
PKF-Mark III rented the RTG RM 20 pile driving rig with HRS 5
hydraulic hammer in August 2016 to support several foundation
elements including 60,000 linear feet of H-piles
The RM 20 took center stage in August 2016. PKF’s decision
to try out ECA’s RM 20 paid off. Its ability to double production
allowed the contractor to eliminate the third set-up altogether.
The contractor further capitalized by putting the unused
second crane to work with a crew of carpenters.
More production, less labour
The RM 20 also reduced manpower. The traditional set-up
requires a crane operator supported by a full crew of pile drivers
whereas the RM 20 requires an operator and a two-person
crew.
The crew has adapted well with the RM 20 as the centerpiece
of the pile driving operation. PKF has two operators,
neither of which are piling rig operators.
“The RM 20 is so self-sufficient you don’t need a key foreman,”
he said. “You just need one person on the ground and
another feeding the machine and that’s your crew.”
The primary operator boarded his first RTG pile driving rig
in summer 2015. ECA dispatched Langan and an ECA factorytrained
service technician to the site at the outset to train the
crew on the RM 20 set the pace for a smooth transition.
“Given his experience with the previous machine (RG
19T), it only took him a couple of days to get acclimated,”
said Keough.
PILING CANADA 65