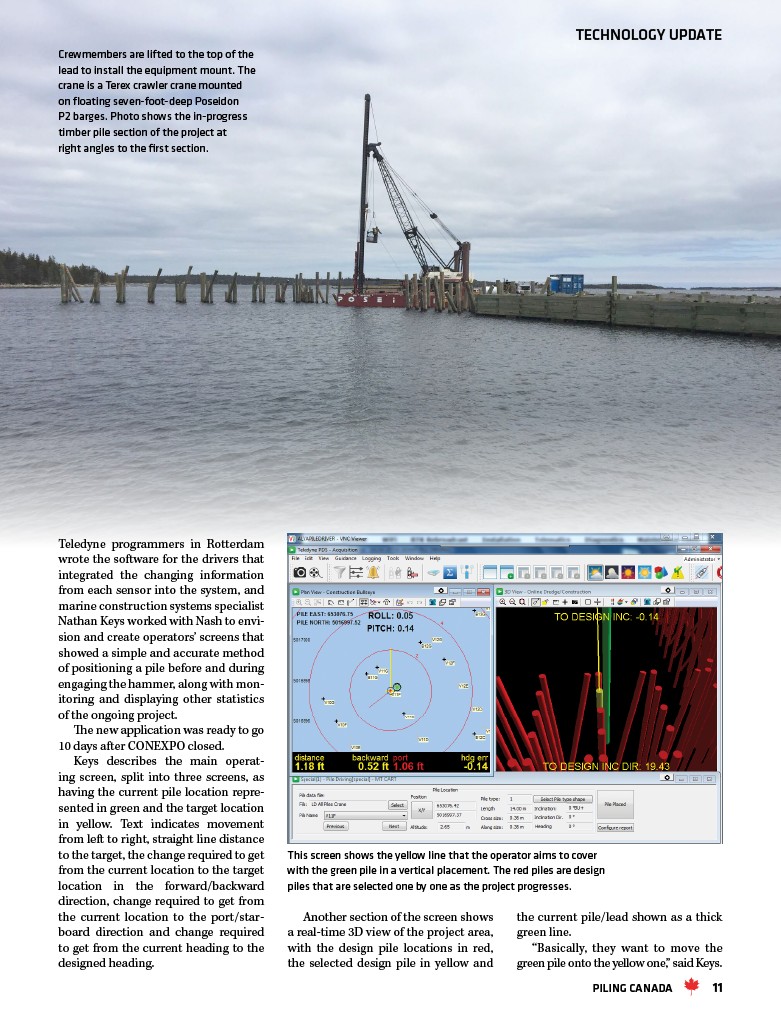
Teledyne programmers in Rotterdam
wrote the software for the drivers that
integrated the changing information
from each sensor into the system, and
marine construction systems specialist
Nathan Keys worked with Nash to envision
and create operators’ screens that
showed a simple and accurate method
of positioning a pile before and during
engaging the hammer, along with monitoring
and displaying other statistics
of the ongoing project.
The new application was ready to go
10 days after CONEXPO closed.
Keys describes the main operating
screen, split into three screens, as
having the current pile location represented
in green and the target location
in yellow. Text indicates movement
from left to right, straight line distance
to the target, the change required to get
from the current location to the target
location in the forward/backward
direction, change required to get from
the current location to the port/starboard
direction and change required
to get from the current heading to the
designed heading.
Another section of the screen shows
a real-time 3D view of the project area,
with the design pile locations in red,
the selected design pile in yellow and
TECHNOLOGY UPDATE
This screen shows the yellow line that the operator aims to cover
with the green pile in a vertical placement. The red piles are design
piles that are selected one by one as the project progresses.
the current pile/lead shown as a thick
green line.
“Basically, they want to move the
green pile onto the yellow one,” said Keys.
Crewmembers are lifted to the top of the
lead to install the equipment mount. The
crane is a Terex crawler crane mounted
on floating seven-foot-deep Poseidon
P2 barges. Photo shows the in-progress
timber pile section of the project at
right angles to the first section.
PILING CANADA 11